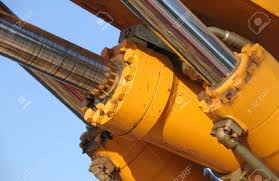
Hydraulic systems are essential in various industries, providing the power needed to perform heavy lifting, precise movements, and fluid control. Central to the effective operation of these systems are hydraulic piston seals, which ensure that hydraulic fluids remain contained and that the system operates efficiently. This article explores hydraulic piston seals in detail, discussing their importance, types, applications, and the relationship with hydraulic bollards.
What Are Hydraulic Piston Seals?
Hydraulic piston seals are components designed to prevent fluid leakage between the moving piston and the cylinder wall in hydraulic systems. They are critical for maintaining pressure, preventing contamination, and ensuring the efficient operation of hydraulic machinery. These seals come in various shapes, sizes, and materials, depending on the specific application and the type of hydraulic fluid used.
Importance of Hydraulic Piston Seals
- Leak Prevention: One of the primary functions of hydraulic piston seals is to prevent the escape of hydraulic fluid from the system. Leaks not only result in fluid loss but can also lead to reduced efficiency and increased operational costs.
- Pressure Maintenance: Seals help maintain the necessary pressure within hydraulic systems. This is crucial for the proper functioning of hydraulic cylinders, pumps, and motors.
- Contamination Control: Hydraulic systems are sensitive to contaminants that can affect performance. Piston seals act as barriers to dirt, dust, and other particles, protecting the hydraulic fluid and components from damage.
- Operational Efficiency: Proper sealing ensures smooth operation and reduces wear and tear on components, extending the life of the hydraulic system and reducing maintenance costs.
Types of Hydraulic Piston Seals
There are several types of hydraulic piston seals, each designed for specific applications and operating conditions. The most common types include:
1. U-Cup Seals
U-cup seals are one of the most widely used seal types in hydraulic applications. They have a U-shaped cross-section and provide a tight fit between the piston and the cylinder wall. The design allows for excellent sealing performance, particularly under low to moderate pressure conditions. U-cup seals are commonly made from rubber, polyurethane, or PTFE (polytetrafluoroethylene).
2. O-Rings
O-rings are circular seals that fit into a groove and are compressed between two surfaces. They are versatile and can be used in various applications, including hydraulic piston seals. O-rings are typically made from elastomeric materials, providing flexibility and resistance to wear. They are best suited for static or low-pressure applications.
3. Lip Seals
Lip seals, also known as rotary seals, are designed with a flexible lip that contacts the surface of the piston or shaft. They are effective at preventing fluid leakage and can accommodate high-speed movements. Lip seals are often used in hydraulic systems with rotating components.
4. Composite Seals
Composite seals combine different materials to enhance sealing performance. They may feature a rubber or elastomeric outer layer for flexibility and a harder core for durability. Composite seals are ideal for high-pressure and high-temperature applications.
5. Hydraulic Oil Seals
Hydraulic oil seals, often used in conjunction with hydraulic piston seals, are designed specifically to prevent hydraulic oil leakage. These seals are critical in maintaining the integrity of hydraulic systems, ensuring that the oil remains contained and does not leak out. They are available in various designs, including lip seals and O-rings, and are made from materials that can withstand the chemical properties of hydraulic fluids.
Materials Used in Hydraulic Piston Seals
The choice of material for hydraulic piston seals is crucial to their performance and longevity. Common materials include:
- Nitrile Rubber (NBR): NBR is a popular choice due to its excellent resistance to hydraulic fluids, oils, and fuels. It is suitable for a wide range of temperatures and offers good mechanical properties.
- Polyurethane: Known for its high abrasion resistance and durability, polyurethane is often used in seals that experience significant wear and tear. It also offers good elasticity and chemical resistance.
- PTFE: PTFE is highly resistant to chemicals and extreme temperatures. It is often used in applications where standard rubber or elastomeric seals would fail. PTFE seals are particularly effective in environments with aggressive fluids.
- Fluoroelastomers: These materials are resistant to high temperatures and a wide range of chemicals, making them suitable for demanding hydraulic applications.
Applications of Hydraulic Piston Seals
Hydraulic piston seals are used in various industries, each with specific applications and requirements:
1. Construction Equipment
Heavy machinery, such as excavators and loaders, relies on hydraulic systems for power and control. Hydraulic piston seals ensure that these machines operate efficiently, providing the necessary force for lifting and moving heavy loads.
2. Automotive Industry
Hydraulic systems are widely used in vehicles for braking, steering, and suspension. Proper sealing in these systems is essential for safety and performance. Hydraulic piston seals play a vital role in maintaining the integrity of automotive hydraulic systems.
3. Manufacturing and Automation
In manufacturing environments, hydraulic systems are used in various machinery and automation equipment. Seals ensure that hydraulic fluids are contained, enhancing the efficiency of processes like injection molding, stamping, and robotics.
4. Agricultural Equipment
Tractors and other agricultural machinery rely on hydraulic systems for various functions, such as plowing and lifting. Hydraulic piston seals help maintain the performance and reliability of these critical machines.
5. Marine Applications
Hydraulic systems are prevalent in marine environments for steering, stabilization, and lifting equipment. Seals must be resistant to corrosion and wear due to exposure to saltwater and harsh conditions.
Installation and Maintenance of Hydraulic Piston Seals
Proper installation and maintenance of hydraulic piston seals are crucial for ensuring their longevity and effectiveness:
1. Installation
- Surface Preparation: Ensure that the surfaces where the seals will be installed are clean and free of debris. Any contaminants can lead to improper sealing and premature failure.
- Correct Sizing: Use seals that are properly sized for the specific application. Incorrect sizes can lead to leaks or excessive wear.
- Lubrication: Before installation, apply a thin layer of compatible hydraulic fluid to the seal to ensure smooth operation and prevent damage during initial movement.
2. Maintenance
- Regular Inspections: Conduct regular inspections of hydraulic systems to check for signs of leakage, wear, or damage. Early detection can prevent costly failures.
- Fluid Quality: Ensure that the hydraulic fluid used is of high quality and compatible with the seals. Contaminated or degraded fluids can lead to seal failure.
- Temperature Monitoring: Monitor operating temperatures to ensure they remain within acceptable limits. Excessive heat can degrade seal materials and compromise their effectiveness.
Conclusion
Hydraulic piston seals are vital components in hydraulic systems, playing a crucial role in preventing leaks, maintaining pressure, and ensuring efficient operation. With various types and materials available, selecting the right seal for a specific application is essential for optimal performance.
The integration of hydraulic oil seal with hydraulic piston seals further enhances the integrity of hydraulic systems, ensuring that hydraulic fluids are contained and functioning effectively. By understanding the importance, types, and applications of hydraulic piston seals, industries can improve their operations, reduce maintenance costs, and enhance the longevity of their hydraulic systems.