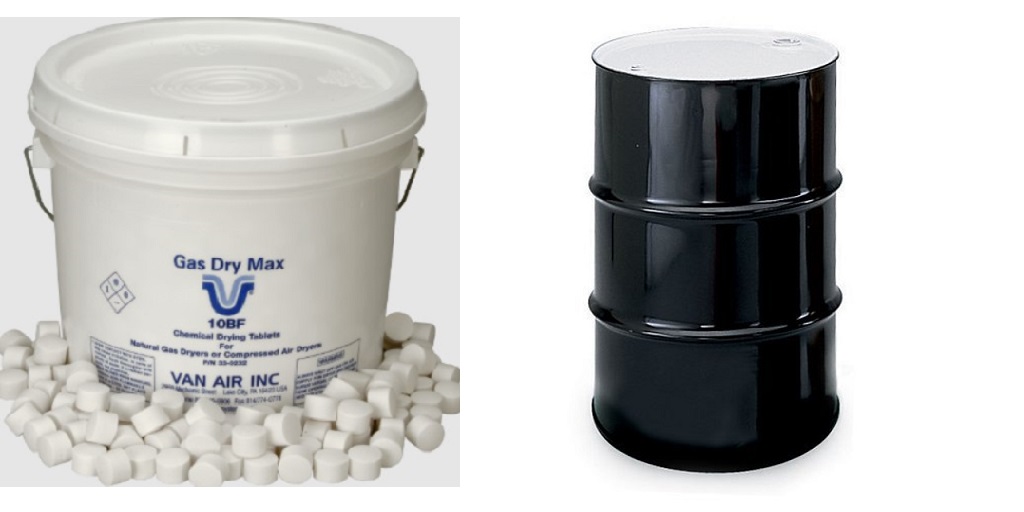
Lithium chloride desiccant is an excellent choice for industrial manufacturers due to its ability to absorb moisture from the air. Its hygroscopic properties ensure dry and efficient processes in various applications, from air conditioning to natural gas dehydration, making it a reliable solution for maintaining optimal conditions.
What Makes Lithium Chloride a Superior Desiccant?
Lithium chloride (LiCl) is renowned for its hygroscopic nature, meaning it actively attracts and retains moisture from its surroundings. This ability makes it an invaluable tool for applications requiring precise moisture control.
- High Absorption Power: Lithium chloride efficiently reduces humidity levels, even in challenging environments.
- Reusable and Cost-Effective: Once saturated, lithium chloride desiccants can be regenerated with heat, releasing the absorbed moisture and making them ready for reuse.
- Enhanced Air Quality: As a liquid solution, lithium chloride can filter microbial contaminants and mold spores from incoming air, ensuring cleaner and safer environments.
What Makes Lithium Chloride Unique?
When selecting a desiccant, it’s essential to match the material to the application. Let’s see how lithium chloride stacks up against other common options:
- Silica Gel: Effective below 77°F (25°C), silica gel absorbs up to 40% of its weight in water. However, it underperforms in higher-temperature environments, limiting its versatility.
- Sodium Chloride: While it can absorb some moisture, sodium chloride lacks the absorption capacity and efficiency of lithium chloride, making it less suitable for industrial applications.
- Lithium Chloride: This desiccant really shines in situations where you need great absorption and efficiency, especially when it’s cooler out. It’s super versatile and is a popular pick for a lot of manufacturers in both industrial and natural gas processes.
Applications That Benefit from Lithium Chloride Desiccants
1. Air Dehumidification Systems
Lithium chloride desiccants play a crucial role in industrial and commercial air dehumidifiers. These systems reduce moisture levels in the air, improving indoor air quality and preventing humidity-related issues like mold growth and equipment corrosion. Industries that prioritize climate control find this desiccant indispensable.
2. Energy-Efficient Air Conditioning
Modern air conditioning systems increasingly incorporate lithium chloride solutions. These liquid desiccant systems control humidity levels while utilizing low-grade heat sources, offering an energy-efficient alternative to traditional air conditioners.
3. Industrial Manufacturing Processes
From drying gases and liquids to maintaining low-humidity environments for precision work, lithium chloride desiccants are a staple in industrial processes. Their reliability and efficiency make them a preferred choice across sectors.
Specialized Use in Natural Gas Processing
Dehydrating natural gas is critical to avoid pipeline corrosion, and hydrate formation, and to meet quality standards. Lithium chloride desiccants shine in this application for several reasons:
- High Hygroscopicity: They efficiently absorb moisture, ensuring gas meets stringent dryness requirements.
- Temperature Efficiency: Unlike other desiccants, lithium chloride performs effectively at lower temperatures, making it suitable for cooler processing environments.
- Pressure Compatibility: Ideal for operations at pressures above 250 psig, lithium chloride offers flexibility across various natural gas scenarios.
- Eco-Friendly: Water-soluble and non-toxic, this desiccant is easy to dispose of, reducing environmental concerns.
Addressing Potential Challenges
While lithium chloride is highly effective, its corrosive nature means careful consideration is needed when designing systems. Materials and coatings that resist corrosion ensure long-lasting performance without compromising the equipment’s integrity.
Why Industrial Manufacturers Rely on Lithium Chloride
Whether used in climate-controlled facilities or gas processing plants, lithium chloride desiccant consistently delivers on efficiency and reliability. Its ability to maintain low humidity levels, regenerate for reuse, and filter contaminants makes it an essential tool for industrial operations.
For businesses seeking top-quality lithium chloride desiccants, Air & Vacuum Process Inc. is the trusted supplier. Offering reliable products designed to meet industrial demands, they provide a one-stop solution for all your moisture control needs.
Don’t Let Moisture Derail Your Operations
Moisture-related issues can lead to costly delays and equipment damage. Let Air & Vacuum Process Inc. help you stay ahead of the humidity curve with their premium desiccant products.
Keep your processes dry and your business thriving—shop lithium chloride desiccants online today.
For more information about Compressed Air Dryer Systems and 50 Gallon Air Compressor Please visit: Air & Vacuum Process Inc.