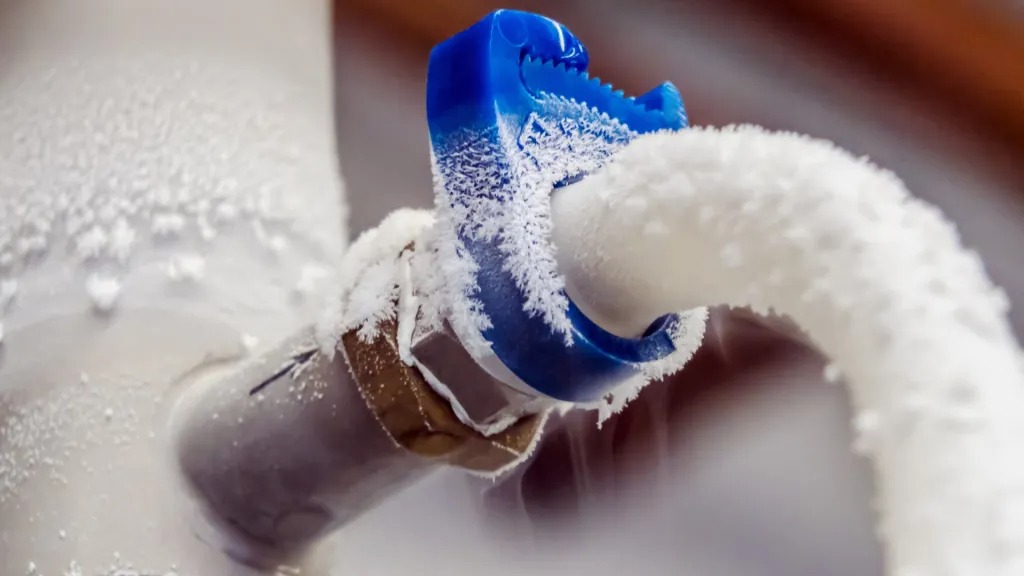
IMARC Group’s “Low-Temperature Silicone Rubber Manufacturing Plant Project Report 2024: Industry Trends, Plant Setup, Machinery, Raw Materials, Investment Opportunities, Cost and Revenue” report provides a comprehensive guide on how to successfully set up a low-temperature silicone rubber manufacturing plant. The report offers clarifications on various aspects, such as unit operations, raw material requirements, utility supply, infrastructural needs, machinery models, labour necessities, transportation timelines, packaging costs, etc.
In addition to the operational aspects, the report also provides in-depth insights into low-temperature silicone rubber manufacturing process, project economics, encompassing vital aspects such as capital investments, project funding, operating expenses, income and expenditure projections, fixed and variable costs, direct and indirect expenses, expected ROI, net present value (NPV), profit and loss account, and thorough financial analysis, among other crucial metrics. With this comprehensive roadmap, entrepreneurs and stakeholders can make informed decisions and venture into a successful low-temperature silicone rubber manufacturing unit.
Request a Sample Report: https://www.imarcgroup.com/low-temperature-silicone-rubber-manufacturing-plant-project-report/requestsample
Note: We are in the process of updating our manufacturing plant reports. If you need the latest data for 2025, including industry trends, plant setup, machinery, raw materials, investment opportunities, cost analysis, and revenue details, Click a request a sample report. The published report will be sent in PDF format via email within 24 to 48 hours.
What is Low-Temperature Silicone Rubber?
Low-temperature silicone rubber is a specialized elastomer known for its exceptional flexibility and durability under extreme cold conditions. This silicone-based material maintains its mechanical properties and elasticity at temperatures as low as -100°C, making it ideal for critical applications in industries like aerospace, automotive, and electronics. It offers excellent resistance to weathering, UV radiation, and chemicals, ensuring long-term performance in challenging environments. Low-temperature silicone rubber is widely used in seals, gaskets, tubing, and insulating materials, where reliability under fluctuating or subzero temperatures is essential. Its versatility and adaptability across industries make it a preferred choice for engineers and designers.
Market Trend and Drivers of Low-Temperature Silicone Rubber:
The growing demand for materials that can withstand harsh environmental conditions is driving the market for low-temperature silicone rubber. Industries such as aerospace and defense are increasingly incorporating this material into components to ensure reliability during high-altitude and extreme weather operations. In the automotive sector, its use in cold climate vehicle parts is gaining traction, addressing the need for performance in freezing temperatures. Additionally, advancements in silicone polymer technologies are enabling the development of more specialized and high-performance low-temperature silicones. As the demand for durable, temperature-resistant materials continues to rise across various industries, the market for low-temperature silicone rubber is expected to witness sustained growth, further supported by its applications in emerging technologies and sustainable product designs.
Key Aspects to Setup a Low-Temperature Silicone Rubber Plant:
- Location to Setup Plant
- Market Research
- Plant Layout
- Construction and Infrastructure
- Equipment/Machinery Procurement
- Documentation and Licenses
- Cost Analysis
Requirements to Setup a Facility:
- Funds
- Machinery
- Lands
Types of Costs to Setup a Factory:
- Land, Location and Site Development Cost
- Plant Layout Cost
- Machinery Requirements and Costs
- Raw Material Requirements and Costs
- Packaging Requirements and Costs
- Transportation Requirements and Costs
- Utility Requirements and Costs
- Human Resource Requirements and Costs
Project Economics:
- Capital Investments
- Operating Costs
- Expenditure Projections
- Revenue Projections
- Taxation and Depreciation
- Profit Projections
- Financial Analysis
Key Questions Answered in the Report:
- How has the low-temperature silicone rubber market performed so far and how will it perform in the coming years?
- What is the market segmentation of the global low-temperature silicone rubber market?
- What is the regional breakup of the global low-temperature silicone rubber market?
- What are the price trends of various feedstocks in the low-temperature silicone rubber industry?
- What is the structure of the low-temperature silicone rubber industry and who are the key players?
- What are the various unit operations involved in a low-temperature silicone rubber manufacturing plant?
- What is the total size of land required for setting up a low-temperature silicone rubber manufacturing plant?
- What is the layout of a low-temperature silicone rubber manufacturing plant?
- What are the machinery requirements for setting up a low-temperature silicone rubber manufacturing plant?
- What are the raw material requirements for setting up a low-temperature silicone rubber manufacturing plant?
- And more…
Browse More Latest Reports:
Dioctyl Phthalate Manufacturing Plant
Elderberry Seed Oil Processing Plant
Heavy Aromatic Naphtha Solvent Manufacturing Plant
Lithium Oxide Manufacturing Plant
How IMARC Can Help?
IMARC Group is a global management consulting firm that helps the world’s most ambitious changemakers to create a lasting impact. The company provide a comprehensive suite of market entry and expansion services. IMARC offerings include thorough market assessment, feasibility studies, company incorporation assistance, factory setup support, regulatory approvals and licensing navigation, branding, marketing and sales strategies, competitive landscape and benchmarking analyses, pricing and cost research, and procurement research.
Services:
- Plant Setup
- Factoring Auditing
- Regulatory Approvals, and Licensing
- Company Incorporation
- Incubation Services
- Recruitment Services
- Marketing and Sales
Contact Us:
IMARC Group
134 N 4th St. Brooklyn, NY 11249, USA
Email: sales@imarcgroup.com
Tel No:(D) +91 120 433 0800
United States: +1-631-791-1145