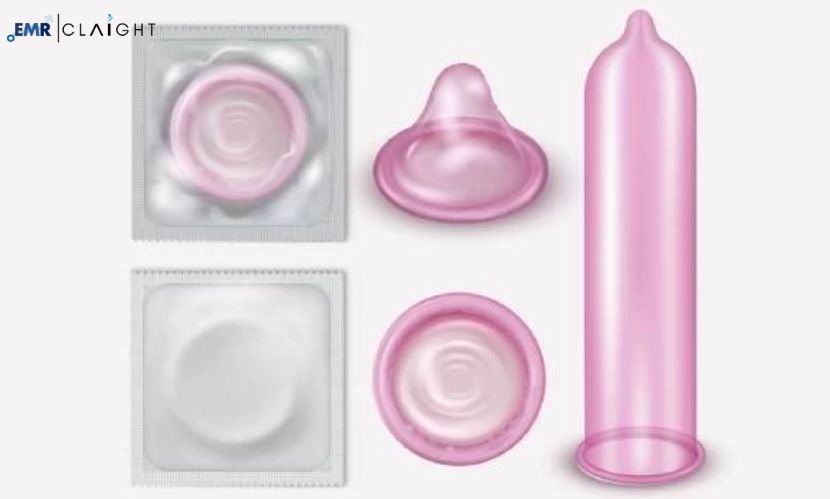
The global demand for condoms, driven by growing awareness about sexual health, contraception, and prevention of sexually transmitted infections (STIs), has resulted in condom manufacturing becoming a vital segment of the healthcare and consumer goods sectors. The Condom Manufacturing Plant Project provides a detailed exploration of the factors influencing the establishment of a condom manufacturing plant, including industry trends, capital investment requirements, price trends, raw materials, plant setup considerations, operating costs, and revenue statistics.
This blog delves into these various aspects, providing a comprehensive understanding of what goes into setting up a condom manufacturing business and how to optimise the process for profitability and sustainability.
-
Industry Trends and Market Demand
The global market for condoms is expected to grow steadily in the coming years, driven by the rising awareness about safe sex, government initiatives for population control, and increasing use of condoms as a preventive measure against STIs. Additionally, the growing demand for condoms in developing countries, coupled with the rising use of female condoms, has opened up new growth opportunities.
Get a Free Sample Report with Table of Contents@ https://www.expertmarketresearch.com/prefeasibility-reports/condom-manufacturing-plant-project-report/requestsample
Several key trends are shaping the condom manufacturing industry:
- Rising Consumer Awareness: With an increased focus on sexual health and disease prevention, consumers are becoming more aware of the importance of condoms. This has led to higher demand for quality and branded condoms.
- Technological Innovations: Manufacturers are incorporating innovative technologies to enhance product quality, improve production efficiency, and meet diverse consumer preferences. These include innovations in condom materials (such as ultra-thin condoms and non-latex varieties), packaging, and manufacturing processes.
- Government Support and Regulatory Compliance: Many governments around the world are increasing their investment in sexual health education and promoting safe sexual practices, which is further driving the demand for condoms.
-
Capital Investment and Financial Considerations
Establishing a condom manufacturing plant requires significant capital investment. The capital required will depend on various factors such as the scale of the plant, the location, and the type of machinery used.
Key financial aspects to consider when setting up a condom manufacturing plant include:
- Initial Capital Investment: The plant setup costs can be divided into the cost of land acquisition, construction, machinery, and other infrastructure. Additionally, the cost of acquiring necessary licences and permits should also be accounted for.
- Machinery and Equipment: The cost of equipment for a condom manufacturing plant can vary depending on the type of condoms produced. Basic equipment includes latex dipping tanks, curing ovens, packaging machines, and testing devices. Advanced technologies for product innovation may also increase the initial investment.
- Operating Expenses: These will include raw material costs, labour costs, energy expenses, and maintenance of machinery. Labour costs vary by location, and energy consumption can be high due to the heating and drying processes involved in manufacturing condoms.
Overall, the capital investment for establishing a condom manufacturing plant can range from a few hundred thousand to several million dollars depending on the scope of the plant.
-
Price Trends in the Condom Industry
The pricing of condoms in the market is influenced by several factors, including production costs, brand positioning, raw material quality, and consumer preferences. Over the years, condom prices have remained relatively stable, with slight fluctuations due to changes in raw material prices and market demand.
Price Trends:
- Premium vs. Standard Condoms: Premium condoms, which feature additional benefits such as ultra-thin materials, flavoured varieties, or larger sizes, are priced higher than standard latex condoms.
- Discounts and Bulk Purchases: The pricing strategy for manufacturers often includes offering bulk deals to retailers and distributors, especially in public health campaigns and government programs aimed at promoting safe sex.
- Raw Material Influence: The price of latex, which is the primary raw material used in condom manufacturing, can fluctuate due to changes in natural rubber prices, which are impacted by weather conditions and global supply-demand dynamics.
Manufacturers must strike a balance between quality and cost efficiency to maintain competitiveness in this price-sensitive market.
-
Manufacturing Process of Condoms
The manufacturing process of condoms is highly automated and involves several key steps, each of which plays a crucial role in ensuring the safety, durability, and comfort of the final product. The process can be broken down into the following stages:
-
Raw Material Preparation:
- Latex Procurement: The primary material used in the manufacturing of condoms is natural rubber latex, which is sourced from rubber trees. Synthetic latex or non-latex materials, such as polyurethane or polyisoprene, are also used in some premium condom varieties.
- Other Additives: Various chemicals, such as stabilizers, vulcanizing agents, and preservatives, are added to the latex to enhance its properties, such as elasticity, durability, and strength.
-
Dipping Process:
- Forming the Condom Shape: The manufacturing process begins with the dipping of glass or stainless steel molds into the liquid latex. The molds are dipped several times to build up the desired thickness of the condom.
- Vulcanization: Once the latex layer is thick enough, the molds are heated to cure the latex, a process known as vulcanization. This makes the rubber more elastic and durable.
-
Testing and Quality Control:
- Electrical Testing: Condoms are tested for small holes or defects by passing an electrical current through them. Any condom that fails this test is discarded.
- Strength and Elasticity Testing: Condoms undergo mechanical testing to check for strength, elasticity, and durability to ensure they meet the required safety standards.
-
Packaging and Distribution:
Once the condoms are fully formed, tested, and dried, they are removed from the molds, lubricated, and packaged. Condoms are typically packaged in individual wrappers to ensure hygiene and easy storage.
-
Raw Materials Required for Condom Manufacturing
The raw materials required for the production of condoms are essential to the final product’s quality. The major raw materials used in condom manufacturing include:
- Natural Rubber Latex: This is the primary material for making traditional condoms. It is derived from rubber trees and has properties of flexibility, elasticity, and strength.
- Synthetic Latex: In some cases, synthetic latex is used to produce condoms for individuals with latex allergies. Synthetic latex provides similar durability and elasticity to natural latex.
- Lubricants: Water-based lubricants, such as glycerin or other chemicals, are applied to the condom to reduce friction during intercourse. These lubricants also help in preserving the condom’s material and quality.
- Coloring Agents: If the condoms are to be coloured, various non-toxic dyes are used to give them aesthetic appeal.
These raw materials are sourced from suppliers and must meet certain quality standards to ensure the safety and effectiveness of the final product.
-
Plant Setup and Location Considerations
Choosing the right location for the condom manufacturing plant is a critical decision that can influence the business’s overall success. Key factors to consider when setting up a condom manufacturing plant include:
- Proximity to Raw Materials: The plant should ideally be located near suppliers of latex or synthetic rubber to reduce transportation costs.
- Labour Availability: Skilled labour is essential for operating the machinery and ensuring the manufacturing process runs smoothly.
- Access to Markets: The plant should be strategically located to allow easy access to key markets, both domestic and international, for distribution.
- Regulatory Compliance: The plant must adhere to local regulations, including health and safety standards, environmental regulations, and labour laws.
-
Operating Costs and Revenue Generation
Operating costs in a condom manufacturing plant include raw material costs, energy consumption, wages, and maintenance costs. The plant’s revenue generation is primarily through the sale of condoms to wholesalers, retailers, and directly to consumers. Revenue growth can be maximized through strategies such as:
- Expanding Product Range: Introducing a wide range of condom types, including premium, flavoured, and extra-thin options, can appeal to a larger audience.
- Retail Partnerships: Collaborating with large retail chains and e-commerce platforms can increase sales volumes.
- Government Contracts: Many governments around the world distribute condoms for free as part of public health programs, creating potential for bulk sales.
Setting up a condom manufacturing plant involves significant financial and operational planning, as well as a thorough understanding of the market dynamics, consumer preferences, and regulatory requirements. By carefully considering industry trends, capital investment, the manufacturing process, raw materials, and operating costs, manufacturers can develop a profitable and sustainable business in the growing global condom market. With the right strategies, manufacturers can position themselves as key players in an industry poised for continued growth and innovation.