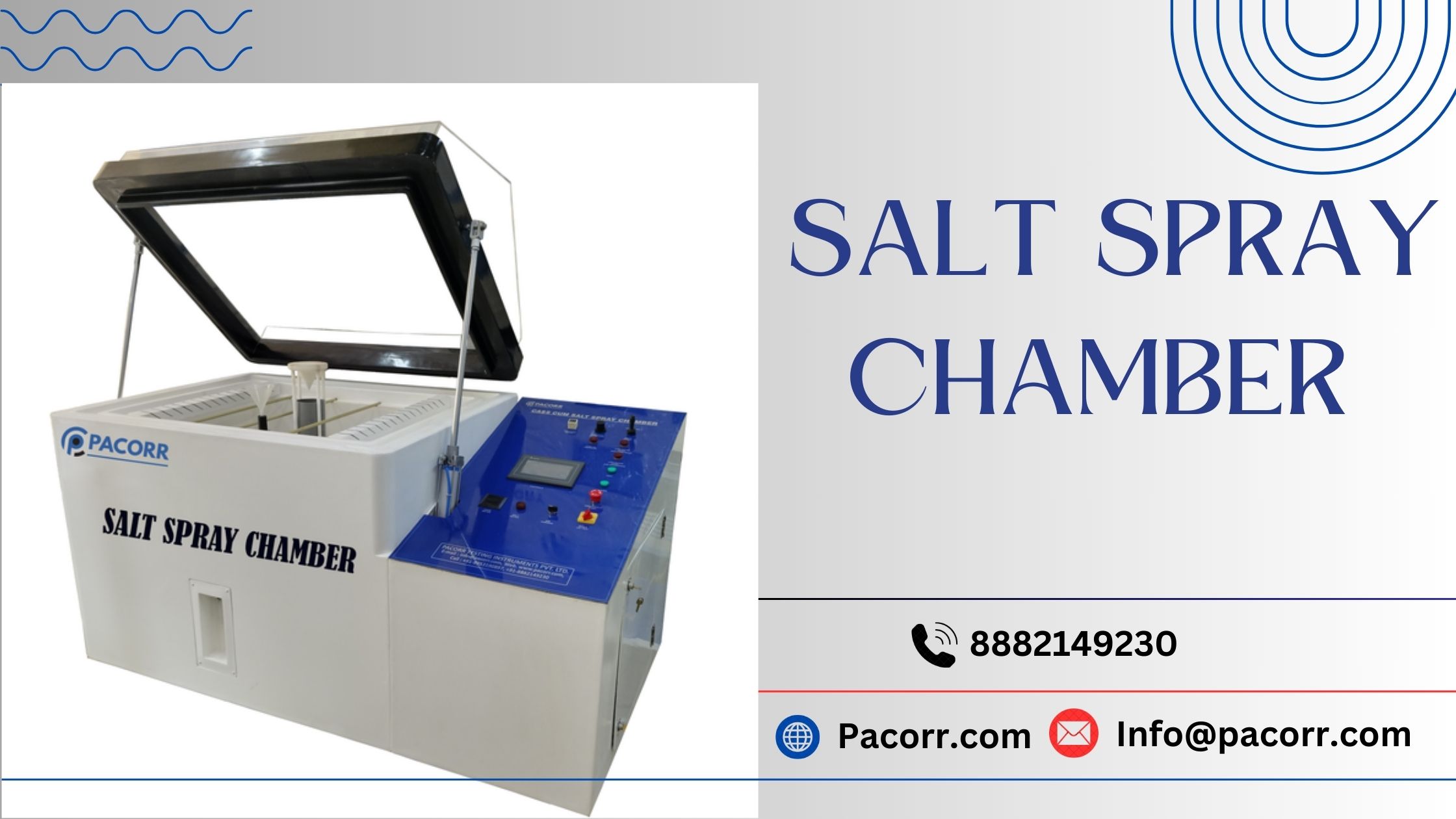
In industries where materials are exposed to tough environments, corrosion resistance is crucial for product longevity. Salt Spray Chamber, also known as salt fog chambers, play a key role in testing how well products stand up to corrosion, which can greatly impact their durability, performance, and appearance. Pacorr provides high-quality salt spray chambers designed for reliable corrosion testing, enabling manufacturers to assess and enhance their products’ resistance to harsh, salty conditions. This article explores what salt spray chambers are, their benefits, and why Pacorr’s chambers are a top choice for precise, efficient testing.
Understanding Salt Spray Chambers
A salt spray chamber is a testing device that creates a controlled, salt-filled environment, allowing manufacturers to simulate years of exposure in a fraction of the time. Inside the chamber, a fine mist of salt solution is generated and distributed, exposing test materials to a simulated corrosive environment. This enables quick identification of potential weak points in materials and coatings, allowing companies to proactively improve their product quality.
Salt spray testing is especially valuable because it compresses what could be years of real-world exposure into a much shorter time frame, helping companies gain insights into material durability quickly.
How Salt Spray Chambers Function
Salt spray chambers operate by misting a salt solution (typically water mixed with sodium chloride) into a sealed environment. Inside, variables like temperature, mist concentration, and humidity are controlled to closely replicate harsh, corrosive conditions. Samples are placed in the chamber, where they undergo a Salt Spray Test Chamber cycle that allows scientists and engineers to observe how materials behave when exposed to salt over extended periods.
Pacorr’s salt spray chambers feature advanced control options, letting users adjust the test environment to meet industry standards and generate consistent, reliable results.
The Importance of Salt Spray Testing
Salt spray testing is an invaluable tool for industries where materials face prolonged exposure to salty or corrosive conditions. It helps manufacturers ensure that their products are built to withstand challenging environments, leading to improved quality, durability, and performance. Key benefits of salt spray testing include:
- Quick Durability Insights: Salt spray testing allows manufacturers to see potential corrosion effects rapidly, providing essential data on a product’s lifespan in just hours or days.
- Enhanced Quality Control: Salt spray chambers help identify potential corrosion issues during the development phase, improving product quality before reaching the customer.
- Cost Savings: By catching and addressing corrosion vulnerabilities early, manufacturers can save on costly recalls, repairs, and replacements.
- Boosted Product Performance: The data from salt spray tests enable companies to optimize material choices and coatings, ensuring better performance and durability over time.
Industries Relying on Salt Spray Testing
Salt spray testing is beneficial across a variety of sectors, where products often face exposure to harsh elements. Here’s how different industries use salt spray testing:
- Automotive Industry: Vehicles are frequently exposed to road salt, rain, and other environmental factors that contribute to corrosion. Salt Spray Chamber Price helps ensure that automotive parts, such as body panels, frames, and exhausts, can endure these conditions.
- Marine and Offshore: For marine applications, where salt exposure is continuous, salt spray testing is crucial to verify the durability of ships, offshore platforms, and related equipment.
- Electronics: Outdoor electronic devices, connectors, and casings are often exposed to moisture and salt. Salt spray testing helps verify that protective coatings on these components will shield them from corrosion, ensuring long-term functionality.
- Construction and Infrastructure: Infrastructure exposed to the elements, particularly in coastal areas, is prone to corrosion. Salt spray testing assists engineers in selecting corrosion-resistant materials for bridges, pipelines, and other structures, ensuring their longevity and safety.
- Consumer Goods: Metal components in items like bicycles, appliances, and furniture are tested for durability using salt spray testing, providing consumers with longer-lasting products.
Standards for Salt Spray Testing
Salt spray testing adheres to globally recognized standards that ensure consistency and accuracy across industries. Pacorr’s Corrosion Test Chamber are designed to meet these standards, delivering precise and reproducible results. Some common testing standards include:
- ASTM B117: This well-known standard is widely used across industries and outlines key guidelines for performing salt spray tests.
- ISO 9227: An international standard for salt spray testing, ensuring testing practices are consistent globally.
- JIS Z 2371: This Japanese standard specifies requirements for salt spray tests in the Japanese manufacturing sector and beyond.
Pacorr’s salt spray chambers are crafted to adhere to these standards, offering accuracy and compatibility with industry needs.
What Makes Pacorr’s Salt Spray Chambers Unique?
Pacorr’s salt spray chambers are recognized for their high performance, ease of use, and durable construction. Here are some features that set Pacorr’s equipment apart:
- Precision Controls: Pacorr chambers allow for detailed control of temperature, mist concentration, and humidity, enabling precise testing environments tailored to industry standards.
- Built to Last: Made from high-quality materials, Pacorr’s chambers are reliable and resilient, making them ideal for high-frequency testing in demanding environments.
- User-Friendly Interface: Pacorr’s chambers feature an intuitive control panel, making it easy for operators to adjust test settings, monitor progress, and obtain accurate results.
- Versatile Sizes: Pacorr offers a range of Salt Spray Chamber sizes to meet the needs of various industries, from compact chambers for small parts to larger units for bulkier components.
- Complies with Global Standards: Pacorr’s chambers are designed to meet ASTM, ISO, and JIS standards, ensuring consistent, high-quality testing results.
Choosing the Right Salt Spray Chamber
When selecting a salt spray chamber, it’s important to consider your specific testing needs to ensure the right fit:
- Size and Capacity: Depending on the types of products you test, you may need a chamber that accommodates multiple or larger samples.
- Control Features: Look for a chamber with comprehensive control options, allowing you to adjust settings like temperature and mist density for precise testing.
- Ease of Maintenance: Reliable performance depends on regular maintenance and calibration. Pacorr’s chambers are designed for easy access, minimizing downtime and ensuring smooth operation.
Limitations of Salt Spray Testing
While salt spray testing provides essential data on corrosion resistance, it cannot replicate all real-world conditions. Factors such as UV exposure, fluctuating temperatures, and varying moisture levels also impact material degradation. To gain a more complete picture of durability, salt spray testing is often used alongside other environmental tests, such as cyclic corrosion and humidity testing.
Conclusion
Salt spray chambers are essential for evaluating how materials respond to corrosive conditions, helping industries produce products that meet high standards for durability and performance. At Pacorr, we are dedicated to providing top-quality Salt Spray Test Chamber that meet international standards and deliver accurate, dependable results. Whether you’re in the automotive, marine, electronics, or consumer goods sector, Pacorr’s salt spray chambers can help you improve quality, reduce costs, and deliver long-lasting products to your customers.