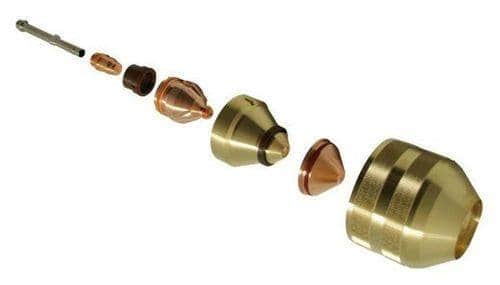
In the competitive global of business reducing, achieving the highest quality cuts with minimum waste is essential to preserving performance and profitability. For specialists and companies counting on plasma cutting technology, the great of consumables used performs a vast position in determining the very last final results. Hypertherm consumables stand out as the favored desire for plenty plasma reducing operations because of their capacity to deliver amazing reducing overall performance, sturdiness, and cost-effectiveness. In this blog, we’ll explore how Hypertherm consumables improve cutting first-class and help reduce waste.
1. Precision Cuts with Hypertherm Consumables
One of the key advantages of the use of Hypertherm consumables is the precision they provide for the duration of the cutting process. Hypertherm’s advanced era guarantees that each consumable is designed to offer constant arc balance, taking into consideration easy and sharp cuts with minimum deviation. Whether you’re working with mild metal, stainless-steel, or aluminum, Hypertherm consumables are engineered to supply accurate effects that meet the highest excellent requirements.
By preserving a consistent cut path, Hypertherm consumables assist reduce the want for transform and scrap fabric. This precision also ensures that the reduce edges are easy, which is vital for programs wherein fit and finish are vital, such as fabrication and assembly.
2. Reduced Heat-Affected Zones
Heat-affected zones (HAZ) can considerably impact the excellent of cuts by way of inflicting warping, discoloration, or even weakening of the cloth being reduce. Hypertherm consumables are in particular designed to lessen the warmth enter into the cloth, hence minimizing the HAZ. This consequences in purifier cuts with much less distortion, ensuring a higher-exceptional finished product.
By decreasing HAZ, Hypertherm consumables also enhance the structural integrity of the cloth, lowering the need for similarly processing, along with grinding or welding. This leads to faster mission turnaround times and less waste from scrap.
3. Maximizing Plasma Cutter Efficiency
Efficiency is some other important component in decreasing waste. Hypertherm consumables are optimized to work seamlessly with Hypertherm plasma cutters, allowing the system to operate at its excellent. The ideal fit among consumables and plasma reducing system guarantees most appropriate arc manipulate and minimal downtime.
Efficient operation way less energy is wasted, and consumables remaining longer. Hypertherm’s superior nozzle and electrode designs improve the overall overall performance of plasma cutters, letting them cut through substances speedy and appropriately without the want for consistent changes or alternative of elements. This leads to fewer consumable changes, less cloth waste, and decreased operational charges through the years.
4. Longer Consumable Life
One of the most notable advantages of Hypertherm consumables is their longevity. Designed with high-quality materials and precision manufacturing, these consumables are built to withstand prolonged use, reducing the frequency of replacements and minimizing the overall cost of ownership.
With longer-lasting consumables, businesses can operate with fewer interruptions, as they don’t have to replace parts as often. This directly translates into less waste, as fewer consumables are disposed of, and fewer cutting errors occur as a result of worn-out or inefficient parts.
5. Improved Cutting Speeds and Reduced Material Wastage
Hypertherm consumables are designed to provide faster cutting speeds without sacrificing quality. Faster cutting speeds not only increase productivity but also reduce the time material is exposed to the cutting process, minimizing the risk of material warping, discoloration, or other defects.
By cutting materials faster and more efficiently, Hypertherm consumables help reduce material waste and increase overall yield. This is especially important in industries where material costs are high, and maximizing every cut can make a significant difference to the bottom line.
6. Cost-Effective Performance
While high-quality consumables may seem like a higher initial investment, the long-term savings from using Hypertherm consumables are undeniable. The improved cutting quality, reduced waste, and extended lifespan of these consumables mean that businesses save money over time, even if the upfront cost is higher than lower-quality alternatives.
By minimizing rework and scrap material, Hypertherm consumables contribute to a more cost-effective operation, ensuring that you get the best return on your investment.
7. Support from EGP Sales
At EGP Sales, we’re committed to presenting our clients with the first-rate merchandise for their plasma reducing needs. By choosing Hypertherm consumable, you’re not most effective making an investment in top rate cutting technology but also receiving top-tier customer service. We assist agencies make the most of their plasma cutting systems, offering expert recommendation, troubleshooting, and supply control to preserve your operation strolling smoothly.
In end, Hypertherm consumables are engineered to enhance slicing first-class and reduce waste by using imparting precision, sturdiness, and efficiency. With their capability to produce smooth cuts, minimize warmness-affected zones, and maximize plasma cutter overall performance, Hypertherm consumables are an invaluable asset to any reducing operation. Investing in those great consumables ensures which you’ll not best enhance the best of your cuts however additionally lessen fabric waste and enhance the profitability of your business.