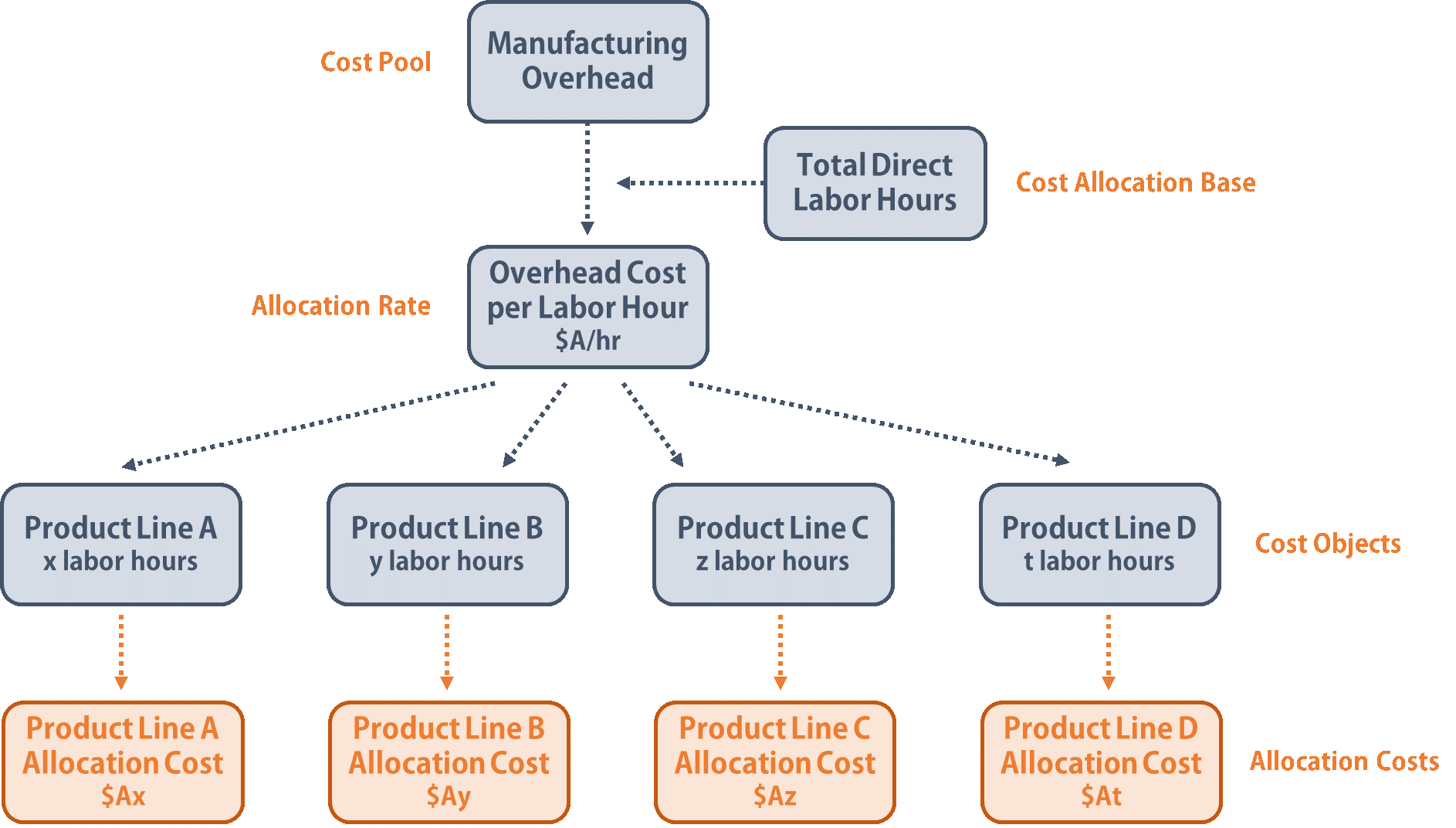
According to a study conducted by McKinsey, these indirect costs account for 8% to 12% of the overall manufacturing costs. Manufacturing cost is the core cost categorization for a manufacturing entity. It encompasses the costs that must be incurred so as to produce marketable inventory. Entities may manufacture several types of products and the sum total of all the costs involved in producing those products is termed as manufacturing cost.
1. Direct materials as a type of manufacturing costs
Standard cost – predetermined cost based on some reasonable basis such as past experiences, budgeted amounts, industry standards, etc. Fixed costs – costs that remain constant regardless of the level of activity. Examples include rent, insurance, and depreciation using the straight line method. Direct materials are raw materials that become an integral part of the finished goods. For the past 52 years, Harold Averkamp (CPA, MBA) hasworked as an accounting supervisor, manager, consultant, university instructor, and innovator in teaching accounting online. He is the sole author of all the materials on AccountingCoach.com.
Top 5 Career Options for Accounting Graduates
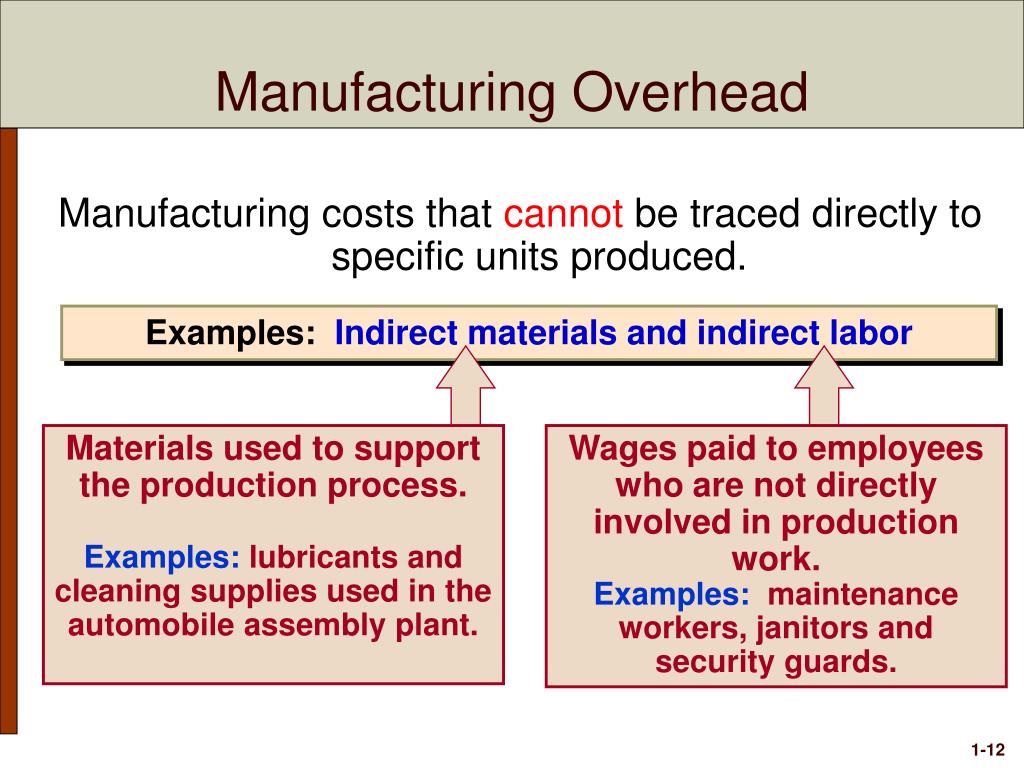
Small, inexpensive items like glue, nails, and masking tape are typically not included in direct materials because the cost of tracing these items to the product outweighs the benefit of having accurate cost data. These minor types of materials, often called supplies or indirect materials, are included in manufacturing overhead, which we define later. Manufacturing costs initially form part of product inventory and are expensed out as cost of goods sold only when the inventory is sold out. Non-manufacturing costs, on the other hand, never get included in inventory rather are expensed out immediately as incurred. This is why the manufacturing costs are often termed as product costs and non-manufacturing costs are often termed as period costs. Examples of direct materials for each boat include the hull, engine, transmission, carpet, gauges, seats, windshield, and swim platform.
Nonmanufacturing Overhead (Explanation Part
Manufacturing businesses calculate their overall expenses in terms of the cost of production per item. That number is, of course, critical to setting the wholesale price of the item. Both of these figures are used to evaluate the total expenses of operating a manufacturing business. The revenue that a company generates must exceed the total expense before it achieves profitability. Direct labor would include the workers who use the wood, hardware, glue, lacquer, and other materials to build tables. With all this valuable information under your belt, you can better track manufacturing costs as they pertain to your workforce.
Understanding non-manufacturing costs is essential for effective budgeting and financial planning as they impact overall profitability and can influence pricing strategies. To help clarify which costs are included in these three categories, let’s look at a furniture company that specializes in building custom wood tables called Custom Furniture Company. Each table is unique and built to customer specifications for use in homes (coffee tables and dining room tables) and offices (boardroom and meeting room tables). The sales price of each table varies significantly, from $1,000 to more than $30,000.
Step #1: Calculate the cost of direct materials
- Whereas, variable direct manufacturing overhead costs include indirect labor, indirect material and utilities.
- Small, inexpensive items like glue, nails, and masking tape are typically not included in direct materials because the cost of tracing these items to the product outweighs the benefit of having accurate cost data.
- Effectively managing expenses in manufacturing isn’t just an option — it’s a necessity.
- Costs that are not related to the production of goods are called nonmanufacturing costs; they are also referred to as period costs.
In the end, management should know whether each product’s selling price is adequate to cover the product’s manufacturing costs, nonmanufacturing costs, and required profit. Manufacturing costs – incurred in the factory to convert raw materials into finished goods. It includes cost of raw materials used (direct materials), direct labor, and factory overhead. On the other hand, a product with a low gross profit may actually be very profitable, if it uses only a minimal amount of administrative and selling expense. Direct labor manufacturing costs is determined by calculating the cost of employees directly responsible for producing the product.
This is where a manufacturing time tracking app, such as Clockify, comes in handy. After manufacturing product X, let’s say the company’s ending inventory (inventory left over) is $500. Therefore, always consult with accounting and tax professionals for assistance with your specific circumstances. Manufacturing costs are also known as factory costs or production costs. Accounting for these costs in market prices could encourage progress toward climate-friendly alternatives. For instance, let’s say the hourly rate a manufacturing company pays to its employees is $30.
A project cost overrun happens when the project costs exceed the budget estimate. That’s why you need a reliable partner to buddy up with and slash your costs. In case you’re spending too many resources on a task or depreciation tax shield depreciation tax shield in capital budgeting project, the option to set budgets in Clockify will give you a detailed insight into how you can better balance those resources. Sunk costs – historical costs that will not make any difference in making a decision.
Manufacturers can compare the costs of making a product using different manufacturing processes. This helps them understand the most efficient process and the investment they need to make for the selected process. A manufacturing company initially purchased individual components from different vendors and assembled them in-house. As the company decided to assemble the components themselves, they found that the costs of managing the assembly line and the transportation were increasing significantly.
Start by making a list of all the direct materials that are used to make the specific product and obtain the cost information for the direct materials you have identified. To calculate the cost of direct materials you need to know the cost of inventory. According to McKinsey’s research, cutting down manufacturing costs, in addition to boosting productivity, is the key for manufacturing companies to remain competitive.
While this is a simplified view of direct labor calculation, accountants also include the benefits, overtime pay, training costs, and payroll taxes when calculating the hourly rate. Mixed costs – costs that vary in total but not in proportion to changes in activity. It basically includes a fixed cost potion plus additional variable costs. An example would be electricity expense that consists of a fixed amount plus variable charges based on usage. Direct materials – cost of items that form an integral part of the finished product. Examples include wood in furniture, steel in automobile, water in bottled drink, fabric in shirt, etc.
Explore high-quality
replica watches in the UK.
Cheap
IWC replica UK wholesale,like IWC replica watches for the best price, top replica watches store.
IWC replica show Swiss luxury replica iwc watch here best cheap price with AAA High quality fake watches.