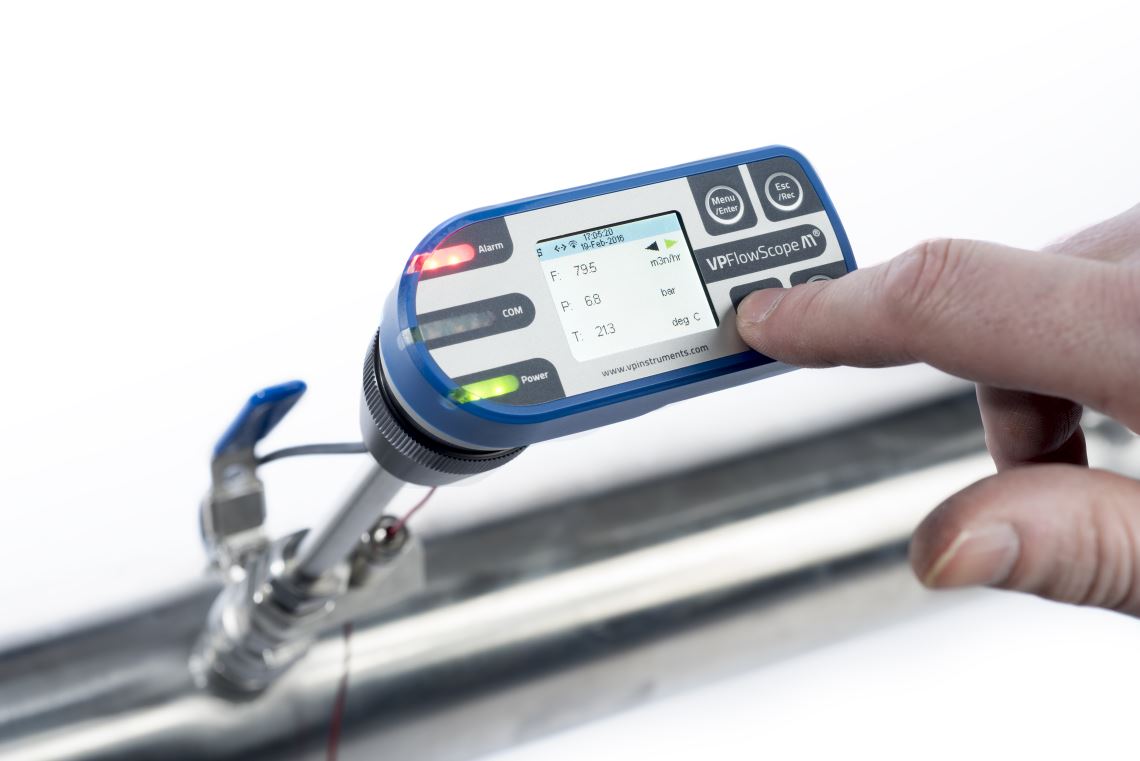
Introduction
Compressed air systems are integral to countless industrial operations, powering everything from assembly lines to pneumatic tools. Yet, even minor leaks in these systems can cause significant energy losses, drive up costs, and degrade overall system performance. Effective leak detection is crucial for maintaining optimal efficiency and reducing operational expenses. In this article, we’ll delve into how to implement effective compressed air leaks detection solutions, providing a comprehensive guide to enhancing your system’s efficiency and saving money.
Benefits of Effective Compressed Air Leak Detection
Implementing effective leak detection is more than just a cost-saving measure—it’s a step towards optimizing your entire system. Here’s how addressing leaks can transform your operations:
1. Cost Savings
- Reduced Energy Consumption: Air leaks force compressors to work harder than necessary, leading to increased energy consumption. By fixing leaks, you decrease the load on your compressors, resulting in lower energy bills. According to industry studies, leak detection and repair can cut energy costs by up to 30%.
- Lower Maintenance and Repair Costs: Identifying leaks early prevents further damage to system components, reducing the need for expensive repairs or replacements. Regular maintenance driven by effective leak detection can extend the lifespan of your equipment and decrease the frequency of major repairs.
2. Enhanced System Efficiency
- Improved Performance and Reliability: A system free of leaks operates more smoothly and reliably. With fewer interruptions and downtime, productivity increases, and operational efficiency is maximized.
3. Environmental Impact
- Reduction in Wasted Resources and Emissions: Leaks result in wasted compressed air, which translates to wasted energy. By minimizing leaks, you contribute to a reduction in carbon emissions and promote a more sustainable operation. This not only benefits the environment but can also enhance your company’s reputation as an environmentally conscious organization.
4. Increased Safety
- Prevention of Potential Hazards and Accidents: Leaks can create hazardous conditions, such as high-pressure jets of air that pose safety risks. Addressing leaks promptly helps maintain a safer work environment, reducing the risk of accidents and ensuring the safety of your workforce.
Step-by-Step Guide to Implementing Effective Leak Detection Solutions
Step 1: Assess Your Current System
- Perform a Baseline Audit: Start with a thorough audit of your current compressed air system. This involves reviewing the system’s efficiency, performance metrics, and historical data to establish a baseline. This baseline will help you understand where inefficiencies lie and where leaks may be occurring.
- Identify Potential Problem Areas: Focus on common leak points such as joints, connections, and valves. High-pressure areas, quick-connect fittings, and pipe supports are often susceptible to leaks. Use historical data to pinpoint areas with frequent issues.
Step 2: Choose the Right Detection Technology
Selecting the appropriate technology for leak detection depends on your specific needs and environment. Here are some effective options:
- Ultrasonic Leak Detectors
- Example: PUREAIR (ASIA) PTE LTD offers advanced ultrasonic leak detectors that can locate leaks with high precision. These devices work by detecting the ultrasonic sound waves produced by escaping air. They are especially useful in noisy environments where other detection methods might fail.
- Explanation: Ultrasonic leak detectors convert high-frequency sound waves into audible sounds, allowing you to pinpoint the exact location of a leak. They are highly sensitive and can detect very small leaks, making them ideal for detailed inspections.
- Infrared Thermography
- Example: VP Instruments provides infrared thermography solutions that detect temperature differences caused by air leaks. This technology visualizes heat variations, making it possible to see leaks that are otherwise invisible.
- Explanation: Infrared thermography captures thermal images of the system, revealing temperature anomalies associated with leaks. This method is non-invasive and can be used to inspect large areas quickly.
- Flow Measurement Tools
- Example: The Flowscope M by VP Instruments measures the flow of compressed air, identifying leaks by monitoring deviations from expected flow rates.
- Explanation: Flow measurement tools monitor the amount of compressed air being used and compare it to expected values. Deviations can indicate leaks or inefficiencies, enabling targeted investigations and repairs.
Step 3: Regular Monitoring and Maintenance
- Establish a Monitoring Schedule: Implement a routine schedule for leak detection checks. Regular inspections help maintain system efficiency and address potential issues before they escalate.
- Use Automated Systems for Continuous Detection: Invest in automated leak detection systems that provide real-time data and alerts. Continuous monitoring helps you stay ahead of leaks and maintain system performance.
Step 4: Analyze Data and Take Action
- Interpret Results from Detection Tools: Analyze the data gathered from your detection tools to identify the exact locations and causes of leaks. Look for patterns and trends that can provide insights into systemic issues.
- Implement Corrective Measures: Once leaks are identified, take immediate action to repair or replace faulty components. Adjust your system to prevent future leaks and ensure long-term efficiency.
Real-Life Examples
Examining how others have successfully implemented leak detection solutions can offer valuable insights:
- Case Study 1: PUREAIR (ASIA) PTE LTD
PUREAIR (ASIA) PTE LTD uses state-of-the-art ultrasonic leak detectors to maintain their compressed air systems’ efficiency. By regularly detecting and addressing leaks, they have achieved significant reductions in energy consumption and maintenance costs. Their proactive approach demonstrates the effectiveness of using advanced detection technologies.
- Case Study 2: VP Instruments
VP Instruments employs their own Flow Measurement Tools to enhance operational efficiency. Accurate flow measurements have enabled them to identify and fix leaks swiftly, resulting in substantial cost savings and improved system reliability. Their use of flow measurement tools highlights the importance of accurate data in leak detection.
- Case Study 3: A Local Manufacturing Company
A local manufacturing company implemented a comprehensive leak detection strategy using a combination of ultrasonic detectors and flow measurement tools. The results were remarkable: they reduced their energy costs by 15% and increased overall system efficiency. This case underscores the benefits of a multi-faceted approach to leak detection.
Conclusion
Compressed air leaks can significantly impact your system’s efficiency and your bottom line. Implementing effective leak detection solutions not only helps in saving money but also enhances system performance, reduces environmental impact, and improves workplace safety. By following the steps outlined above and leveraging advanced technologies, you can optimize your compressed air systems and achieve lasting benefits.
Call-to-Action
Ready to enhance your leak detection strategy? Contact experts like PUREAIR (ASIA) PTE LTD or VP Instruments to explore advanced detection solutions tailored to your needs. Invest in the right technology today and start reaping the benefits of a more efficient and cost-effective compressed air system. For more information and resources, check out our recommended tools and services.