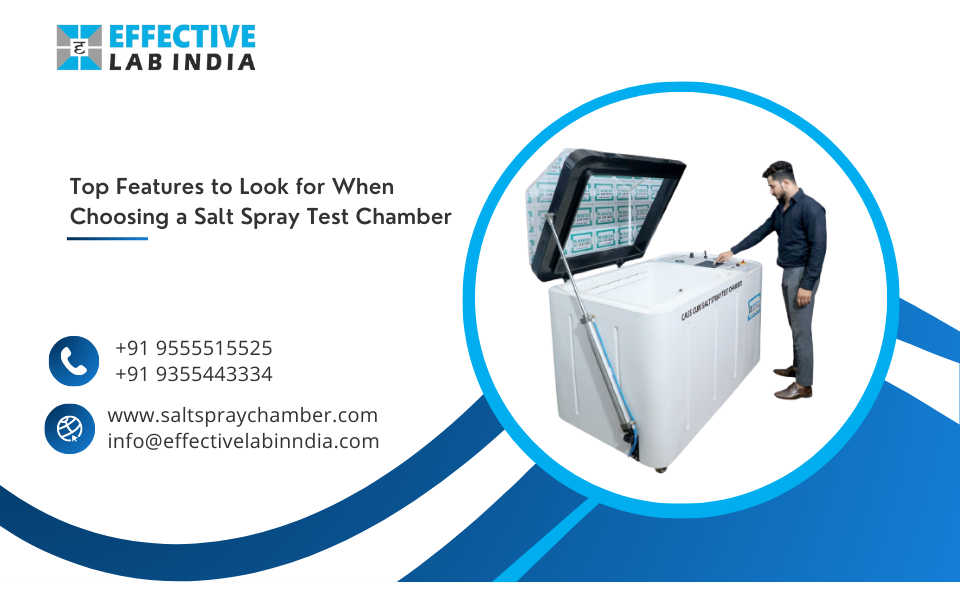
The most important part of quality control in some sectors, including manufacturing, aerospace, and automobiles, is corrosion testing. Understanding the key components of a
salt spray test chamber serves as essential for selecting one that provides accurate and trustworthy testing results.
What is a Salt Spray Test Chamber?
One piece of specialized equipment used to assess the corrosion resistance of materials, coatings, and surface treatments is a
salt spray test chamber. To assess test specimens’ endurance over time, a fine mist of saline solution is sprayed upon them in a controlled atmosphere, simulating harsh conditions. This testing technique, which is frequently employed in sectors like industrial, aerospace, and automotive, guarantees product dependability and adherence to global standards like ISO 9227 and ASTM B117.We go over the most important factors to take into account when choosing a salt spray test chamber to suit your testing requirements below.
1. Chamber Size and Capacity
The
salt spray test chamber’s size and capacity are among the first things to be assessed. You will want a chamber that can hold the size and quantity of test specimens, depending on your testing needs. Choose chambers that can be sized to accommodate bulk testing for large industrial applications.
Important Points to Remember:Internal Dimensions: Make sure your largest test sample can fit inside the chamber and that there is enough airflow to allow for uniform exposure.
Sample Holder Configuration: For flexible sample positioning, look for racks or supports that can be adjusted.
2. Construction Material
The materials used in the test chamber’s construction have a major impact on its lifetime and durability. Since extremely corrosive solutions are used in salt spray testing, the chamber needs to be able to withstand chemical wear.
Important Points to Remember:Fibreglass Reinforced Plastic (FRP): Offers superior resistance to corrosion.
Stainless Steel Components: Components made of stainless steel guarantee easy maintenance and rust-free operation.
PVC coating: An additional layer of defence against exposure to salt is provided by PVC coating.
3. Temperature Control System
Establishing constant testing conditions requires an accurate temperature control system. Selecting a chamber with an advanced thermostat is important since temperature variations could affect results from tests.
Important Points to Remember:Digital Display: Makes it simple to keep an eye on and modify temperature settings.
Automatic Regulation: A constant temperature range, usually between 35°C and 45°C, is maintained by automatic regulation.
Uniform Distribution: For precise test conditions, make sure the chamber heats up uniformly.
4. Salt Spray Generation System
The salt spray generating system, which ensures a constant and consistent fog dispersion, is the central component of any
salt spray test chamber.Important attributes:
Nozzle Design: A top-notch atomising nozzle enables uniform fog production free from blockages.
Fog Density Control: Modifiable parameters to regulate spray density and salt concentration.
Reservoir Capacity: During extended tests, a large reservoir minimises the need for refills.
5. Compliance with International Standards
The test chamber must adhere to pertinent international testing standards in order to provide accurate and widely recognised results.
Common Guidelines:- The most frequently accepted standard for evaluating salt spray is ASTM B117.
- Salt spray testing for metallic coatings and non-metallic substrates is covered by ISO 9227.
- A common Japanese standard for evaluating automotive parts is JIS Z 2371.
6. User-Friendly Interface
Usability is a crucial factor, particularly for labs that perform tests frequently. An intuitive user interface streamlines processes and lowers the learning curve for novice users.Features to Examine:
Touchscreen Controls: Touchscreen controls are simple to use and require little training.
Programmable Options: Convenient pre-set testing cycles.
Notifications & Alerts: Notifications of low salt levels or temperature variations.
7. Advanced Data Logging
To monitor and evaluate testing parameters, contemporary salt spray test chambers are outfitted with data logging features.Benefits:
Real-Time Monitoring: Throughout tests, access real-time data.
Storage and Retrieval: Maintain testing records for research and auditing needs.
USB and Wi-Fi Connectivity: Data may be transferred to external devices with ease thanks to USB and Wi-Fi connectivity.
8. Safety Features
Working with corrosive materials should always be done safely. Select a chamber with strong safety features to safeguard the apparatus and the operator.Essential Safety Elements:
Overheat Protection: When the temperature rises too high, the system automatically shuts down.
Sealed Enclosure: Stops corrosive fog from leaking.
Emergency Stop Button: During emergencies, the emergency stop button rapidly stops operations.
9. Maintenance Requirements
Your
salt spray test chamber’s long-term performance depends on how easy it is to maintain. Think about models with straightforward maintenance and cleaning procedures.Features that Make Maintenance Simple:
- Drainage System: Easy chamber cleaning thanks to rapid drainage.
- Removable Components: Removable pieces make cleaning and part replacement easier.
- Access panels: Make it simple to enter internal parts for maintenance or examination.
10. Cost and Warranty
Lastly, take into account the total cost, which includes maintenance, operation, and installation. A thorough warranty safeguards your investment and provides peace of mind.
Factors affecting costs:
Initial Investment: Look for the best deal by comparing features and pricing points.O
perational Costs: Take into account consumables like water and salt as well as energy efficiency.
Warranty Coverage: Seek out extended warranties that include both labour and parts.
Conclusion
Selecting the
best salt spray test chamber requires carefully weighing its characteristics to make sure it fits your unique testing requirements. You may make an informed choice that ensures accurate and dependable findings by taking into account elements like chamber size, material durability, standard compliance, and sophisticated features.