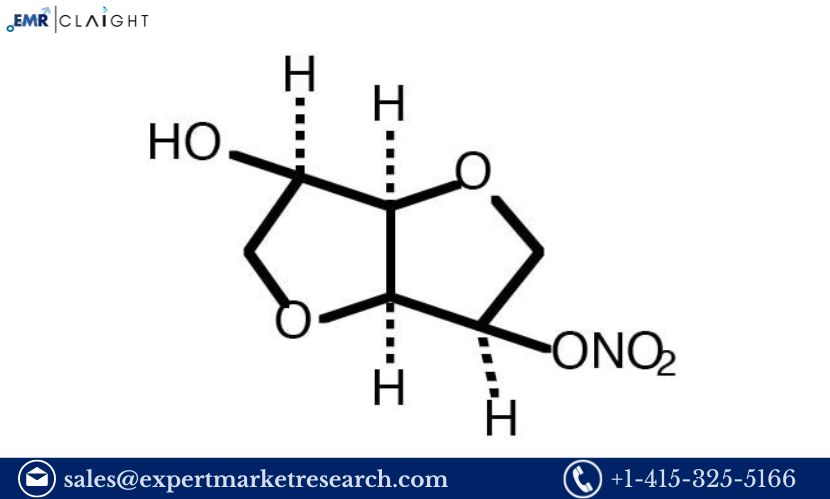
Introduction
The pharmaceutical industry is continually advancing to meet the needs of patients with cardiovascular conditions. Isosorbide Mononitrate (ISMN) is a key medication used in the treatment of angina pectoris and other heart-related issues. As a vital component in managing heart disease, the demand for ISMN is rising, making the establishment of a dedicated manufacturing plant increasingly important. This Isosorbide Mononitrate Manufacturing Plant Project Report provides a comprehensive overview of the Isosorbide Mononitrate Manufacturing Plant Project, covering its scope, design, benefits, challenges, and answering common questions.
Project Overview
Isosorbide Mononitrate is a nitrate vasodilator that helps in relieving angina by relaxing blood vessels and improving blood flow to the heart. Given its critical role in treating cardiovascular diseases, a specialized manufacturing plant for ISMN ensures a consistent and high-quality supply of this essential drug. The project involves multiple stages, from initial feasibility studies through to full-scale production, including design, construction, equipment procurement, and operational setup.
Key Phases of the Project
Feasibility Study
The feasibility study is the first step in the project and includes:
- Market Analysis: Assessing the demand for ISMN, identifying potential competitors, and understanding market trends.
- Cost Estimation: Calculating the financial requirements for construction, equipment, and ongoing operational costs.
- Site Selection: Choosing a location that offers logistical advantages, meets regulatory requirements, and has access to necessary resources.
- Risk Assessment: Identifying potential risks and developing strategies to address them.
Get a Free Sample Report with Table of Contents @
Design and Planning
Once feasibility is confirmed, the project moves to design and planning:
- Facility Design: Designing the plant layout to accommodate production, quality control, storage, and administrative functions while adhering to Good Manufacturing Practices (GMP).
- Equipment Procurement: Selecting and procuring machinery for the production of ISMN, including reactors, filtration systems, and packaging equipment.
- Regulatory Approvals: Obtaining approvals from health authorities and environmental agencies to ensure compliance with safety and environmental regulations.
Construction
The construction phase involves building the physical infrastructure of the plant:
- Building Infrastructure: Constructing production areas, laboratories, clean rooms, and storage facilities.
- Utilities Installation: Setting up essential systems such as water, electricity, HVAC (heating, ventilation, and air conditioning), and waste management.
Equipment Installation and Testing
Following construction, the focus shifts to installing and testing equipment:
- Installation: Setting up machinery and ensuring all systems are integrated and functional.
- Testing: Conducting rigorous tests to verify that equipment performs to specifications and meets quality standards.
Operational Setup
In this phase, the plant prepares for full-scale production:
- Staff Recruitment and Training: Hiring skilled personnel and providing training on manufacturing processes, quality control, and safety protocols.
- Standard Operating Procedures (SOPs): Developing and implementing SOPs for all manufacturing processes to ensure consistency and compliance with regulatory standards.
Launch and Scale-Up
With the plant fully operational, it transitions to the production phase:
- Pilot Production: Running initial production batches to test processes and resolve any issues.
- Full-Scale Production: Scaling up to meet production targets while continuously monitoring and optimizing processes.
Benefits of the Project
Enhanced Supply: A dedicated ISMN manufacturing plant will ensure a reliable and consistent supply of the drug, addressing market demands and reducing potential shortages.
Economic Impact: The project will generate job opportunities and stimulate the local economy through construction and operational activities.
Quality Assurance: With a focus on high-quality production, the plant will meet stringent standards, ensuring the safety and efficacy of ISMN.
Innovation: Implementing advanced technologies and efficient production processes can lead to cost reductions and improved manufacturing practices.
FAQs
What is Isosorbide Mononitrate used for?
Isosorbide Mononitrate is used primarily for the prevention and treatment of angina pectoris (chest pain) caused by coronary artery disease. It helps to relax blood vessels and improve blood flow to the heart.
Why is a dedicated Isosorbide Mononitrate manufacturing plant necessary?
A dedicated manufacturing plant ensures a consistent, high-quality supply of ISMN, which is essential for meeting the therapeutic needs of patients with cardiovascular conditions. It also allows for specialized production processes that adhere to stringent quality and safety standards.
What are the key considerations for site selection?
Key considerations include proximity to raw materials and distribution channels, access to skilled labor, compliance with regulatory requirements, and availability of infrastructure and utilities.
How long does it take to build and start operations at a new Isosorbide Mononitrate manufacturing plant?
Typically, it takes 18 to 24 months from planning and design through to full-scale production. This timeline includes feasibility studies, construction, equipment installation, and testing.
What are Good Manufacturing Practices (GMP)?
Good Manufacturing Practices (GMP) are guidelines designed to ensure that products are consistently produced and controlled according to quality standards. They cover all aspects of production, from raw materials to equipment and personnel.
How does the project impact the local community?
The project creates job opportunities, stimulates local businesses through construction and operational phases, and contributes to the local economy. Additionally, by improving access to a critical medication, the plant benefits public health.
Related Reports
https://www.expertmarketresearch.com/reports/astaxanthin-market
https://www.expertmarketresearch.com/reports/weapon-night-sight-market/market-size
https://www.expertmarketresearch.com/reports/satellite-communication-market
Media Contact:
Company Name: Claight Corporation
Contact Person: Lewis Fernandas, Corporate Sales Specialist — U.S.A.
Email: sales@expertmarketresearch.com
Toll Free Number: +1–415–325–5166 | +44–702–402–5790
Address: 30 North Gould Street, Sheridan, WY 82801, USA
Website: www.expertmarketresearch.com
Aus Site: https://www.expertmarketresearch.com.au