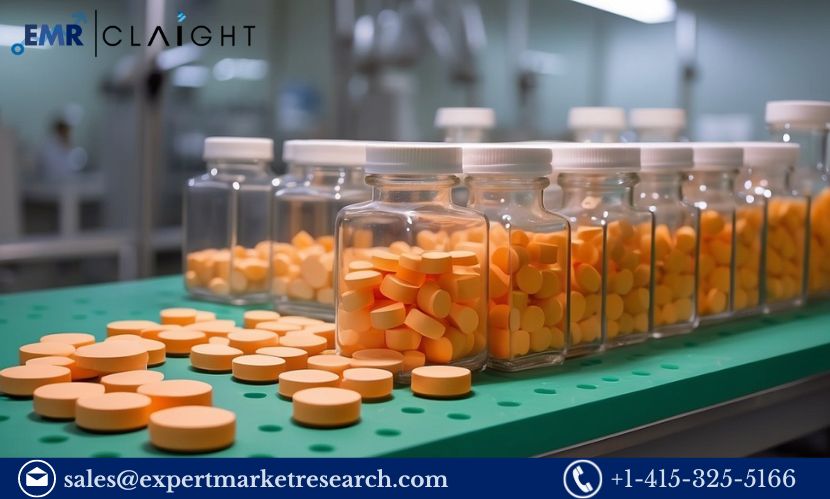
Understanding Ranolazine (Ranexa)
Ranolazine is an anti-anginal agent that helps manage chronic angina by improving blood flow to the heart and reducing the heart’s workload. It works by inhibiting the late phase of the sodium current in cardiac cells, which helps stabilize heart function. It is commonly prescribed for patients who have not achieved adequate symptom control with other angina treatments.
Key Benefits of Ranolazine:
- Effective Angina Relief: Ranolazine helps reduce chest pain and improve exercise tolerance.
- Improved Quality of Life: It enhances patients’ ability to perform daily activities without experiencing angina.
- Versatility: It can be used in combination with other anti-anginal therapies for better results.
Get a Free Sample Report with Table of Contents @ https://www.expertmarketresearch.com/prefeasibility-reports/ranolazine-ranexa-manufacturing-plant-project-report/requestsample
Key Considerations for Setting Up a Ranolazine Manufacturing Plant
- Market Research and Feasibility Study
Conducting thorough market research is crucial before establishing a Ranolazine manufacturing plant. Analyze the current demand for Ranolazine, evaluate the competitive landscape, and identify potential customers, including hospitals, clinics, and pharmaceutical distributors. A feasibility study will help assess the economic viability of the project, including market size, growth trends, and investment requirements.
- Location and Infrastructure
Choosing the right location for your manufacturing plant is essential. Consider the following factors:
- Proximity to Raw Materials: Ensure access to key ingredients and chemical reagents used in Ranolazine production.
- Logistics: Select a location with efficient transportation networks for both raw materials and finished products.
- Infrastructure: The facility should have necessary utilities such as water, electricity, and waste management systems.
- Technology and Equipment
The production of Ranolazine involves several specialized technologies and pieces of equipment. Key components include:
- Reactors: For chemical synthesis of Ranolazine from its precursors.
- Purification Units: To remove impurities and ensure the final product meets pharmaceutical standards.
- Formulation Equipment: For producing various dosages forms, such as tablets or extended-release formulations.
- Quality Control Labs: To conduct rigorous testing and ensure the product’s safety and efficacy.
Investing in state-of-the-art technology and maintaining rigorous quality control are crucial for ensuring high-quality production.
- Raw Materials and Supply Chain
The primary raw materials for Ranolazine production include:
- Chemical Precursors: Used in the synthesis of Ranolazine.
- Excipients: Substances used in tablet formulation and stabilization.
Establish strong relationships with suppliers to secure high-quality raw materials and ensure a steady supply. Efficient supply chain management is also critical for maintaining production schedules and controlling costs.
- Regulations and Compliance
Adherence to regulatory requirements is essential for operating a pharmaceutical manufacturing plant. Key compliance areas include:
- Good Manufacturing Practices (GMP): Ensure that all production processes meet stringent quality and safety standards.
- Regulatory Approvals: Obtain necessary approvals from regulatory agencies, such as the FDA or EMA, for manufacturing and marketing Ranolazine.
- Environmental and Safety Regulations: Implement measures to minimize environmental impact and ensure workplace safety.
Regular audits and inspections will help maintain compliance and uphold the quality of the manufacturing process.
- Production Process
The production process for Ranolazine generally involves several stages:
- Chemical Synthesis: The initial stage involves synthesizing Ranolazine from its chemical precursors using reactors and specialized reagents.
- Purification: The synthesized compound is purified to remove any impurities and achieve the desired potency.
- Formulation: Ranolazine is then formulated into its final dosage form, such as tablets or extended-release capsules.
- Quality Control: Rigorous testing is conducted to ensure the final product meets all quality and safety standards.
Implementing robust quality control measures throughout the production process is crucial for ensuring the efficacy and safety of the final product.
- Marketing and Sales Strategy
Developing a strong marketing and sales strategy is key to the success of your Ranolazine manufacturing plant. Consider the following:
- Target Markets: Identify potential customers, including hospitals, clinics, and pharmacies.
- Promotion: Utilize marketing channels such as industry conferences, medical journals, and digital platforms to promote your product.
- Distribution: Establish efficient distribution channels to ensure timely delivery of Ranolazine to healthcare providers and patients.
Building strong relationships with healthcare professionals and pharmaceutical distributors can also help enhance market presence and sales.
- Financial Planning
A detailed financial plan is essential for managing your plant’s budget and ensuring profitability. Key components include:
- Initial Investment Costs: Expenses related to plant setup, equipment purchase, and raw materials.
- Operational Expenses: Costs for labor, maintenance, utilities, and ongoing raw material procurement.
- Revenue Projections: Forecasted sales based on market research and pricing strategies.
- Profit Margins: Analysis of potential profit margins and return on investment.
Securing funding through loans, investors, or grants may be necessary to support the initial setup and ongoing operations.
Frequently Asked Questions (FAQ)
What are the primary uses of Ranolazine (Ranexa)?
Ranolazine is primarily used to treat chronic angina by improving blood flow to the heart and reducing the heart’s workload. It helps manage chest pain and improve exercise tolerance in patients with angina who have not responded adequately to other treatments.
What are the main challenges in setting up a Ranolazine manufacturing plant?
Key challenges include navigating complex regulatory requirements, ensuring the safety and efficacy of the product, and managing the production of a high-quality pharmaceutical compound. Additionally, maintaining compliance with Good Manufacturing Practices (GMP) and addressing potential supply chain issues are crucial.
How can I ensure the quality of Ranolazine production?
Ensuring high-quality production involves implementing rigorous quality control measures, such as testing raw materials, monitoring production processes, and conducting final product testing. Investing in advanced technology and adhering to Good Manufacturing Practices (GMP) are also essential.
What are the regulatory requirements for manufacturing Ranolazine?
Manufacturing Ranolazine requires compliance with Good Manufacturing Practices (GMP) and obtaining regulatory approvals from agencies such as the FDA or EMA. This includes meeting standards for quality, safety, and efficacy, as well as adhering to environmental and safety regulations.
How much does it cost to set up a Ranolazine manufacturing plant?
The cost of setting up a Ranolazine manufacturing plant can vary significantly based on factors such as plant size, location, technology, and scale of production. Initial investments can range from several million to tens of millions of dollars. A detailed feasibility study will provide a more accurate
Media Contact:
Company Name: Claight Corporation
Contact Person: Lewis Fernandas, Corporate Sales Specialist — U.S.A.
Email: sales@expertmarketresearch.com
Toll Free Number: +1–415–325–5166 | +44–702–402–5790
Address: 30 North Gould Street, Sheridan, WY 82801, USA
Website: www.expertmarketresearch.com
Aus Site: https://www.expertmarketresearch.com.au/