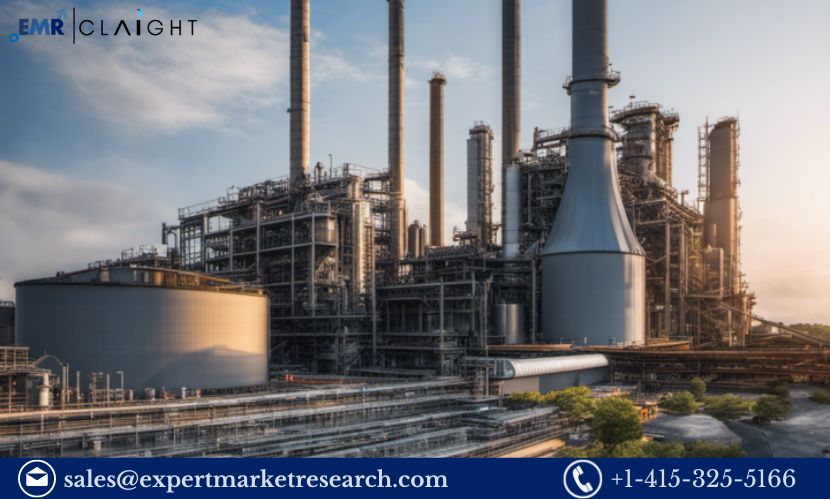
Introduction
Zinc nitrite is an inorganic compound used in various applications, primarily as a corrosion inhibitor, in the production of dyes, and in the food industry as a curing agent. With the growing emphasis on corrosion prevention in various industrial sectors and the increasing demand for food preservation techniques, establishing a zinc nitrite manufacturing plant can be a lucrative business opportunity. This Zinc Nitrite Manufacturing Plant Project Report explores the critical components of setting up such a facility, including market analysis, project feasibility, raw material sourcing, manufacturing processes, and financial projections.
Market Analysis
Demand and Supply
The demand for zinc nitrite is influenced by several factors:
- Corrosion Control Needs: Industries such as construction, automotive, and marine are increasingly seeking effective corrosion inhibitors to prolong the lifespan of their products. Zinc nitrite is known for its effectiveness in preventing rust and corrosion on metal surfaces.
- Food Industry Applications: In the food industry, zinc nitrite serves as a curing agent, particularly in meat products. The growing processed food market, along with an emphasis on food safety and preservation, boosts the demand for zinc nitrite.
- Dye Production: Zinc nitrite is also used in the manufacturing of dyes and pigments, which are essential in various industries including textiles and cosmetics.
Target Market
The primary target markets for zinc nitrite include:
- Construction and Automotive Industries: Manufacturers looking for effective corrosion inhibitors.
- Food Processing Companies: Producers of cured meats and other processed foods requiring preservatives.
- Chemical Manufacturers: Companies producing dyes and pigments that require zinc nitrite as a raw material.
Competition
The market for zinc nitrite includes several established players, but there are still opportunities for new entrants. Companies that can offer high-quality products at competitive prices, along with reliable supply chains and customer service, will likely succeed in this market.
Get a Free Sample Report with Table of Contents @
Project Feasibility
Location
Choosing the right location for the manufacturing plant is crucial. Key factors to consider include:
- Proximity to Raw Material Suppliers: Being close to suppliers of zinc and nitrous acid can reduce transportation costs and ensure timely delivery.
- Transportation Infrastructure: Good access to transportation networks is essential for the efficient distribution of the finished product.
- Utility Availability: Reliable access to electricity, water, and other utilities is necessary for manufacturing operations.
- Labor Pool: Availability of skilled labor for operations and management is critical.
Technology
The production of zinc nitrite involves several technological considerations:
- Synthesis Process: Zinc nitrite is typically produced by the reaction of zinc oxide or zinc carbonate with nitrous acid. This process requires precise control of temperature and pH levels to ensure high yield and purity.
- Purification Techniques: The synthesized product may require purification through filtration or crystallization to remove impurities and achieve the desired quality.
- Quality Control Systems: Implementing robust quality control measures is essential to ensure that the final product meets industry standards for purity and safety.
Regulatory Compliance
Compliance with industry regulations is critical for the success of the manufacturing plant. This includes:
- Obtaining Necessary Licenses: Securing all required permits from local and international regulatory bodies.
- Good Manufacturing Practices (GMP): Adhering to GMP guidelines to ensure product quality and safety throughout the manufacturing process.
- Environmental Regulations: Implementing waste management and emission control measures to comply with environmental standards.
Raw Material Sourcing
The primary raw materials required for the production of zinc nitrite include:
- Zinc Oxide or Zinc Carbonate: The main sources of zinc used in the synthesis of zinc nitrite.
- Nitrous Acid: Required for the chemical reaction to produce zinc nitrite.
- Other Chemicals: Depending on the synthesis route, additional reagents may be necessary for the production process.
Establishing strong relationships with reliable suppliers will ensure a consistent and high-quality supply of raw materials.
Manufacturing Process
Overview
The manufacturing process for zinc nitrite generally includes the following steps:
- Raw Material Preparation: All necessary chemicals are prepared and tested for quality before the synthesis process.
- Synthesis Reaction: Zinc oxide or zinc carbonate is reacted with nitrous acid under controlled conditions to produce zinc nitrite.
- Purification: The crude zinc nitrite may be purified through filtration or crystallization to remove any impurities and achieve the desired purity levels.
- Quality Control: Rigorous testing is conducted at each stage of production to ensure compliance with industry standards for potency and purity.
- Packaging: The final product is packaged in suitable containers to protect it during transportation and storage.
Quality Assurance
Implementing a robust quality assurance system is essential to maintain product integrity. Regular testing for purity, moisture content, and other quality parameters should be conducted to ensure compliance with customer specifications.
Financial Projections
Capital Investment
The initial capital investment for establishing a zinc nitrite manufacturing plant can vary widely, typically ranging from $3 million to $8 million. Factors influencing this range include plant size, technology used, and location.
Operating Costs
Key operating costs include:
- Raw Materials: Costs for zinc oxide or zinc carbonate and nitrous acid.
- Labor Costs: Salaries and wages for skilled employees.
- Utilities: Expenses for electricity, water, and other utilities.
- Maintenance: Regular maintenance costs for machinery and equipment.
- Marketing and Distribution: Costs associated with promoting and distributing the product.
Revenue Projections
With effective marketing strategies and a solid customer base, a zinc nitrite manufacturing plant can achieve a break-even point within 2-3 years. Profit margins typically range from 15% to 25%, depending on market conditions and operational efficiency.
FAQs
1. What is zinc nitrite used for?
Zinc nitrite is primarily used as a corrosion inhibitor, a curing agent in food processing, and in the production of dyes and pigments.
2. How is zinc nitrite manufactured?
Zinc nitrite is produced by reacting zinc oxide or zinc carbonate with nitrous acid, followed by purification and packaging.
3. What are the primary raw materials for producing zinc nitrite?
The main raw materials include zinc oxide or zinc carbonate and nitrous acid.
4. What regulations must be adhered to in zinc nitrite manufacturing?
Manufacturers must comply with Good Manufacturing Practices (GMP), obtain necessary licenses, and meet environmental regulations to ensure product quality and safety.
5. What are the financial risks associated with starting a zinc nitrite manufacturing plant?
Key risks include fluctuations in raw material prices, regulatory compliance costs, and competition in the market. Conducting thorough market research and financial forecasting can help mitigate these risks.
Related Reports
https://www.expertmarketresearch.com/reports/medium-voltage-motors-market
https://www.expertmarketresearch.com/reports/lubricating-oil-additives-market
https://www.expertmarketresearch.com/reports/gelatin-market
Media Contact:
Company Name: Claight Corporation
Contact Person: Lewis Fernandas, Corporate Sales Specialist — U.S.A.
Email: sales@expertmarketresearch.com
Toll Free Number: +1–415–325–5166 | +44–702–402–5790
Address: 30 North Gould Street, Sheridan, WY 82801, USA
Website: www.expertmarketresearch.com
Aus Site: https://www.expertmarketresearch.com.au