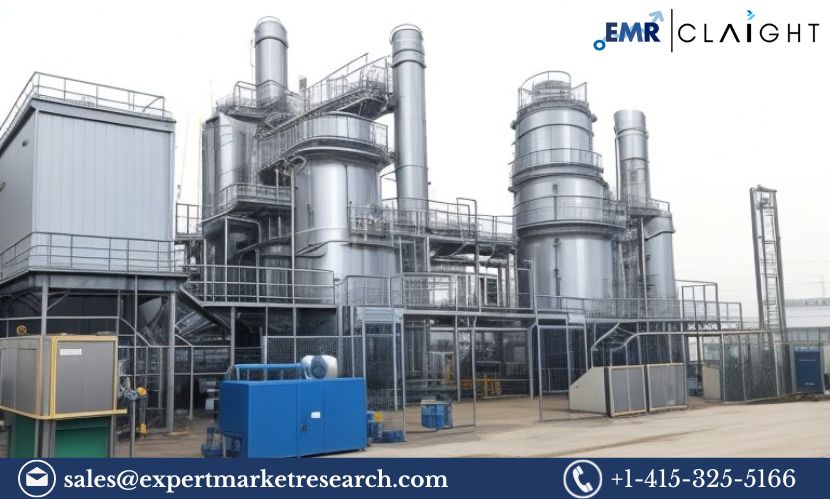
Introduction
Calcium sulfite is an inorganic compound used primarily in industries like water treatment, construction, and paper manufacturing. Its primary function is as a reducing agent and a scavenger of oxygen, making it useful in applications where oxygen removal is necessary, such as in treating boiler water and preserving food. As industries continue to grow, the demand for calcium sulfite has remained steady, presenting a viable business opportunity for manufacturers. This article provides a detailed Calcium Sulfite Manufacturing Plant Project Report, outlining the production process, critical considerations, and answers to common questions for potential investors and those interested in calcium sulfite manufacturing.
Overview of Calcium Sulfite and Its Uses
Calcium sulfite (CaSO₃) is a white, powdery compound commonly used for its oxygen-scavenging properties. It has various industrial applications, including:
- Water Treatment: Calcium sulfite is widely used in the treatment of boiler water to remove dissolved oxygen, which helps prevent corrosion in pipes and equipment.
- Construction: In the construction industry, calcium sulfite can be used as a filler in gypsum board and other building materials.
- Paper Manufacturing: The compound is used in the production of paper, particularly in processes that involve sulfite pulping.
- Food Preservation: Although not widely used today, calcium sulfite was historically employed as a food preservative to prevent spoilage by inhibiting microbial growth.
Due to its oxygen-scavenging abilities, calcium sulfite is highly valued in industries where oxygen control is essential. Additionally, calcium sulfite plays a role in flue gas desulfurization processes, where it helps remove sulfur dioxide from emissions in industrial plants, contributing to pollution control.
Get a Free Sample Report with Table of Contents @
Overview of the Calcium Sulfite Manufacturing Process
Manufacturing calcium sulfite involves a chemical reaction between calcium compounds and sulfur dioxide. Here’s a general outline of the production process:
- Raw Material Preparation: The process begins with calcium sources such as calcium hydroxide (slaked lime) or calcium carbonate (limestone), which are prepared for reaction with sulfur dioxide gas.
- Reaction with Sulfur Dioxide: The calcium compound is then exposed to sulfur dioxide (SO₂) in a controlled environment. This reaction results in the formation of calcium sulfite. The reaction is carefully managed to ensure complete conversion and to control the release of gases.
- Filtration and Separation: Once the reaction is complete, the mixture is filtered to separate the calcium sulfite from any unreacted materials or by-products. This step ensures the product’s purity and prepares it for further processing.
- Drying and Milling: The calcium sulfite is dried to remove any excess moisture and may be ground into a fine powder if required for specific applications. This step depends on the intended use of the final product, as some applications require powdered calcium sulfite while others may use granules or larger particles.
- Packaging and Storage: Finally, the calcium sulfite is packaged in moisture-resistant containers to maintain its stability during storage and transportation. Proper labeling and storage conditions are essential to ensure the compound remains uncontaminated and ready for industrial use.
Each step in the production process is closely monitored to ensure the product meets quality standards and complies with safety regulations, given the reactive nature of sulfur dioxide gas.
Key Considerations for Setting Up a Calcium Sulfite Manufacturing Plant
Establishing a calcium sulfite manufacturing plant involves several important factors to ensure efficient and safe operations:
- Location: The plant should ideally be located near sources of raw materials, such as limestone or calcium hydroxide, and have access to sulfur dioxide supplies. Proximity to transportation networks is also beneficial for distributing the product to various industries. Additionally, the facility must comply with environmental regulations due to the use of sulfur dioxide in production.
- Technology and Equipment: Calcium sulfite production requires specialized equipment, including reactors for the chemical reaction, filtration systems, and drying units. Automated control systems can help monitor the reaction conditions and ensure safety. High-quality, durable equipment contributes to consistent production standards and enhances overall efficiency.
- Labor and Skilled Workforce: A trained workforce is essential to operate the equipment safely and handle chemicals such as sulfur dioxide. Employees should be trained in chemical handling, equipment operation, and quality control to maintain high production standards. Regular training programs help workers stay up-to-date on best practices and safety protocols.
- Safety and Environmental Considerations: Handling sulfur dioxide requires strict safety protocols due to its toxicity and reactivity. Proper ventilation, personal protective equipment (PPE), and emergency response systems are essential to ensure a safe working environment. Environmental considerations include waste management and emissions control to comply with local regulations and minimize the plant’s impact on the surrounding area.
Financial Considerations and Cost Overview
Setting up a calcium sulfite manufacturing plant requires a significant financial investment. Key expenses include land acquisition, facility construction, equipment purchase, and workforce training. Ongoing operational costs include raw materials, energy, waste management, and regulatory compliance. Proper budgeting and financial planning are crucial to managing these costs effectively and ensuring the plant’s long-term profitability.
Investing in efficient equipment and production techniques can help reduce operational costs over time, while implementing sustainable practices and emissions control systems can enhance environmental compliance and minimize potential fines or penalties.
Market Potential and Industry Trends
The market for calcium sulfite is driven by demand from various sectors, particularly water treatment and flue gas desulfurization. Key industry trends include an increased focus on environmental sustainability and pollution control, as regulations around emissions become more stringent. Additionally, calcium sulfite’s role in reducing corrosion in boiler systems and extending the lifespan of industrial equipment contributes to its steady demand in industrial applications.
Understanding these trends can help businesses identify growth opportunities and align their production strategies with market needs. The demand for calcium sulfite is expected to remain stable, especially in regions where industrial expansion and pollution control are prioritized.
Steps to Implement the Project
The process of establishing a calcium sulfite manufacturing plant generally involves the following phases:
- Planning and Permitting: This initial phase involves selecting a suitable site, obtaining necessary permits, and ensuring compliance with environmental and safety regulations. A detailed project plan helps define the scope, timeline, and budget for the project.
- Facility Construction and Equipment Setup: Once planning is complete, the construction phase begins. This includes building the facility and installing specialized equipment for the reaction, filtration, and drying processes.
- Testing and Training: After construction, the equipment undergoes testing to ensure it operates correctly. Employees receive training on equipment operation, safety protocols, and quality control measures to ensure they can work safely and efficiently.
- Operational Readiness: The final stage involves preparing the plant for full-scale production. Quality control systems are put in place, and production processes are optimized to meet the output and quality requirements for calcium sulfite.
FAQs
- What are the main uses of calcium sulfite?
Calcium sulfite is used in water treatment to remove dissolved oxygen, in the construction industry as a filler, in paper manufacturing, and in pollution control applications such as flue gas desulfurization. - How is calcium sulfite produced?
Calcium sulfite is produced by reacting a calcium compound (such as calcium hydroxide or calcium carbonate) with sulfur dioxide. The reaction results in calcium sulfite, which is then purified, dried, and packaged. - What are the safety considerations for a calcium sulfite manufacturing plant?
Safety considerations include proper ventilation, personal protective equipment, and emergency response systems. The handling of sulfur dioxide requires strict adherence to safety protocols to minimize health and environmental risks. - What are the environmental considerations for a calcium sulfite plant?
Environmental considerations include managing emissions from sulfur dioxide and adhering to local regulations. Waste management and emissions control systems help reduce the plant’s environmental impact. - What factors affect the cost of setting up a calcium sulfite manufacturing plant?
Key cost factors include land acquisition, facility construction, equipment purchase, labor, raw materials, and regulatory compliance. Effective financial planning can help manage these costs and support long-term profitability.
Related Reports
fraud detection and prevention market
spain residential real estate-market
remote sensing software market
Media Contact:
Company Name: Claight Corporation
Contact Person: Lewis Fernandas, Corporate Sales Specialist — U.S.A.
Email: sales@expertmarketresearch.com
Toll Free Number: +1–415–325–5166 | +44–702–402–5790
Address: 30 North Gould Street, Sheridan, WY 82801, USA
Website: www.expertmarketresearch.com
Aus Site: https://www.expertmarketresearch.com.au