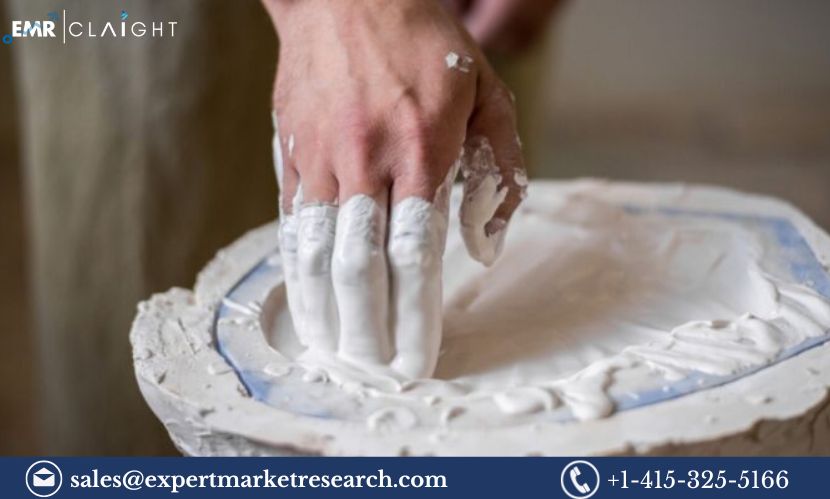
Introduction
Plaster of Paris (PoP) is a versatile building material widely used in construction, interior design, and arts and crafts. Known for its quick-setting properties and smooth finish, PoP is ideal for creating intricate designs and moulds. The establishment of a Plaster of Paris manufacturing plant presents a lucrative opportunity due to the increasing demand for this material across various industries. This Plaster of Paris Manufacturing Plant Project Report provides a detailed overview of setting up a Plaster of Paris manufacturing plant, covering essential aspects such as raw materials, production processes, equipment requirements, investment considerations, and market potential.
Market Overview
Demand Drivers
The demand for Plaster of Paris has been steadily increasing due to several factors:
- Construction Industry: With rapid urbanisation and infrastructural development, the construction sector is a primary consumer of PoP for wall finishing, false ceilings, and decorative moulding.
- Art and Craft: PoP is widely used in arts and crafts, including sculpture making, decorative items, and educational projects.
- Health Sector: The medical field utilises PoP for making orthopaedic casts and moulds, contributing to its steady demand.
Key Market Trends
- Sustainable Construction: The growing trend towards sustainable and eco-friendly building materials has boosted the demand for PoP, as it is non-toxic and recyclable.
- Innovative Applications: Emerging applications in interior design, such as light-weight wall panels and ceiling designs, are expanding the market for Plaster of Paris.
- Growth in Emerging Markets: Developing economies are witnessing increased construction activities, thereby augmenting the demand for PoP.
Get a Free Sample Report with Table of Contents@
Manufacturing Process
Raw Materials
The primary raw material for producing Plaster of Paris is gypsum. Other materials may include:
- Water: Required for the mixing process.
- Additives: Various additives may be used to enhance properties such as setting time, strength, and workability.
Production Steps
- Gypsum Mining: The process begins with the extraction of gypsum, which is the raw material for Plaster of Paris.
- Crushing and Grinding: The mined gypsum is crushed and ground into a fine powder.
- Calcination: The ground gypsum powder is heated in a calcination furnace at controlled temperatures to remove water content, converting it into hemihydrate gypsum, which is Plaster of Paris.
- Mixing: The calcined powder is mixed with water to create a slurry. Additives can also be incorporated during this step to improve properties.
- Moulding and Setting: The slurry is poured into moulds to achieve desired shapes. It sets quickly, hardening into a solid form.
- Drying and Curing: The set plaster is dried in controlled conditions to remove excess moisture and enhance strength.
- Quality Control: Rigorous quality checks are conducted to ensure the product meets industry standards regarding strength, purity, and consistency.
- Packaging: The final product is packaged in bags or bulk containers for distribution to various markets.
Quality Control Measures
To ensure the quality of Plaster of Paris, manufacturers should implement:
- Material Testing: Regular testing of raw gypsum for purity and quality before processing.
- Product Testing: Testing of the final product for setting time, compressive strength, and texture.
- Environmental Monitoring: Ensuring that the manufacturing process adheres to environmental regulations to minimise pollution.
Investment Requirements
Capital Expenses
Setting up a Plaster of Paris manufacturing plant involves initial investments in:
- Facility Setup: A suitable location that complies with zoning laws and has access to utilities like water and electricity.
- Machinery and Equipment: Essential equipment includes crushers, grinders, calcination furnaces, mixers, moulds, and packaging machines.
- Storage: Adequate storage for raw materials and finished products is necessary.
Operational Costs
Ongoing operational costs include:
- Raw Material Sourcing: Regular procurement of gypsum and other materials.
- Labour Costs: Wages for skilled workers and staff for production and quality control.
- Utilities: Expenses related to water, electricity, and maintenance of machinery.
Site Selection
Key considerations for choosing a site for the Plaster of Paris manufacturing plant include:
- Proximity to Gypsum Sources: A location near gypsum mines can significantly reduce transportation costs.
- Accessibility to Markets: Being close to construction hubs and distribution networks facilitates efficient delivery of the final product.
- Infrastructure Availability: Access to reliable infrastructure, such as roads and utilities, is crucial for smooth operations.
Regulatory Compliance
Establishing a Plaster of Paris manufacturing plant requires adherence to various regulations:
- Safety Standards: Compliance with local safety regulations to ensure worker safety and product quality.
- Environmental Regulations: Adhering to environmental laws related to emissions and waste disposal to minimise ecological impact.
- Health Standards: Ensuring that the production process meets health regulations to safeguard the end users.
FAQ
What is Plaster of Paris used for?
Plaster of Paris is used in construction for wall finishes, decorative mouldings, and in arts and crafts for creating sculptures and casts.
How is Plaster of Paris manufactured?
The manufacturing process involves mining gypsum, crushing and grinding it, calcination, mixing with water, moulding, and drying.
What equipment is necessary for a Plaster of Paris manufacturing plant?
Essential equipment includes crushers, grinders, calcination furnaces, mixers, moulds, and packaging machines.
What are the main costs involved in setting up a PoP plant?
The main costs include facility setup, machinery, raw materials, labour, and ongoing operational expenses.
What regulations must be followed for a Plaster of Paris manufacturing plant?
Compliance with safety standards, environmental regulations, and health standards is mandatory for producing Plaster of Paris.
Related Reports
https://www.expertmarketresearch.com/reports/security-market
https://www.expertmarketresearch.com/reports/barbeque-grill-market
https://www.expertmarketresearch.com/reports/oilfield-services-market
Media Contact:
Company Name: Claight Corporation
Contact Person: Lewis Fernandas, Corporate Sales Specialist — U.S.A.
Email: sales@expertmarketresearch.com
Toll Free Number: +1–415–325–5166 | +44–702–402–5790
Address: 30 North Gould Street, Sheridan, WY 82801, USA
Website: www.expertmarketresearch.com
Aus Site: https://www.expertmarketresearch.com.au