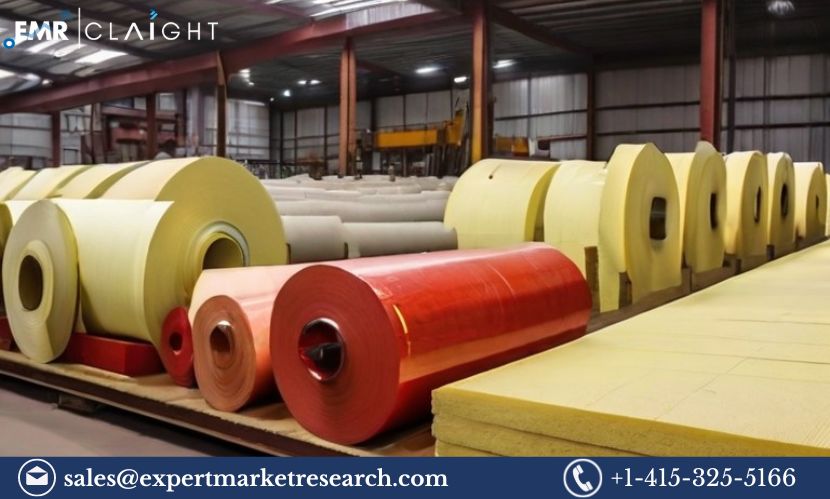
Introduction
The Rock Wool Insulation Manufacturing Plant Project Report provides a comprehensive analysis of setting up a facility dedicated to producing rock wool insulation, a highly effective and versatile material known for its thermal, acoustic, and fire-resistant properties. Rock wool, also called mineral wool or stone wool, is made from volcanic rock such as basalt, making it a sustainable and eco-friendly insulation option. With increasing demand for energy-efficient and fire-safe construction materials, investing in a rock wool insulation manufacturing plant presents a promising business opportunity. This article covers every aspect of establishing a rock wool insulation plant, including the manufacturing process, market potential, equipment requirements, financial considerations, regulatory approvals, and frequently asked questions (FAQs).
Overview of Rock Wool Insulation
Rock wool insulation is produced by melting volcanic rock and other raw materials at extremely high temperatures, spinning the molten rock into fibers, and then shaping these fibers into various forms such as batts, boards, and rolls. It has several benefits that make it popular in the construction industry:
- Thermal Insulation: Rock wool has excellent thermal insulation properties, helping to reduce heat loss and maintain a consistent indoor temperature.
- Acoustic Insulation: The dense fibrous structure effectively absorbs sound, making it ideal for noise control in homes, offices, and industrial buildings.
- Fire Resistance: As a non-combustible material, rock wool can withstand temperatures up to 1,000°C, adding a vital layer of fire protection to structures.
- Moisture Resistance: Unlike other insulation materials, rock wool does not absorb water, preventing mold growth and maintaining its insulating properties in humid environments.
Get a Free Sample Report with Table of Contents @
Market Potential for Rock Wool Insulation
Several factors are driving the demand for rock wool insulation in various sectors:
- Energy Efficiency Regulations: Governments worldwide are promoting energy-efficient buildings, mandating the use of insulation to reduce energy consumption and greenhouse gas emissions. Rock wool is a key material for meeting these energy standards.
- Fire Safety Standards: As fire safety codes become stricter, particularly for high-rise buildings and industrial structures, rock wool’s fire-resistant properties make it a preferred choice.
- Sustainable Construction: With growing awareness of environmental sustainability, builders are increasingly choosing eco-friendly materials like rock wool, which is made from natural rocks and often incorporates recycled content.
- Growth in Construction: Rapid urbanization, particularly in developing countries, is fueling demand for insulation materials. Rock wool is used in residential, commercial, and industrial construction to enhance energy efficiency and comfort.
- Soundproofing Needs: In densely populated urban areas, controlling noise pollution is critical. Rock wool’s sound absorption properties make it ideal for soundproofing applications in homes, offices, and industrial settings.
Manufacturing Process of Rock Wool Insulation
Establishing a rock wool insulation manufacturing plant involves several technical steps that require specialized machinery and skilled labor. Below is an outline of the production process:
- Raw Material Preparation: The primary raw materials include basalt, diabase, or other volcanic rocks. A small amount of coke or anthracite is added to fuel the melting process.
- Melting: The raw materials are fed into a cupola furnace, where they are heated to temperatures above 1,500°C. The rocks melt into a molten state.
- Fiber Formation: The molten rock is spun at high speed through a spinning machine, forming thin fibers, similar to the way cotton candy is made.
- Binding and Curing: The fibers are sprayed with a binding agent, usually a resin, to help hold them together. The material is then cured in an oven at high temperatures to set the binder and form the final product.
- Shaping and Cutting: The cured wool is cut into batts, boards, or rolls, depending on the intended application. The products are cut to standard sizes for easy installation.
- Quality Control: Throughout the process, quality control checks are performed to ensure the insulation meets industry standards for thermal, acoustic, and fire resistance.
- Packaging and Distribution: The finished products are packed, labeled, and shipped to distributors or directly to construction sites.
Equipment and Machinery Required
Setting up a rock wool insulation manufacturing plant requires significant investment in equipment. The primary machinery includes:
- Cupola Furnace: To melt the raw materials at high temperatures.
- Spinning Machine: To spin the molten rock into fibers.
- Conveyor System: To transport the fibers through different stages of production.
- Curing Oven: To set and solidify the fibers after binding.
- Cutting and Shaping Machines: To cut the insulation into the desired forms (batts, boards, or rolls).
- Packaging Machines: For packaging the final product for transportation and distribution.
Investment and Financial Considerations
Setting up a Rock Wool Insulation Manufacturing Plant requires substantial financial investment. Here’s a breakdown of the key financial elements involved:
- Initial Capital Investment: The total investment depends on the scale of the plant and the machinery used. A medium-scale plant might require an initial investment of $3 million to $10 million.
- Operating Costs: Ongoing expenses include raw material procurement, labor costs, energy consumption, equipment maintenance, and transportation.
- Profit Margins: Rock wool manufacturing offers competitive profit margins, typically ranging from 20% to 40%. Factors such as production efficiency, market demand, and cost management influence profitability.
- Return on Investment (ROI): Depending on market conditions and production efficiency, the ROI can be achieved within 2 to 5 years, making this a lucrative venture in the insulation industry.
Regulatory Compliance
Establishing a rock wool insulation manufacturing plant involves adhering to various regulations and obtaining necessary approvals:
- Environmental Permits: The manufacturing process involves emissions and energy-intensive operations. Plants must obtain permits related to air quality, emissions, and waste management.
- Health and Safety Regulations: Due to the high-temperature processes and handling of hazardous materials, manufacturers must comply with safety standards to protect workers.
- Building and Zoning Permits: Depending on the location, manufacturers may need to acquire building permits and comply with local zoning laws.
FAQs
-
What is rock wool insulation used for?
Rock wool insulation is primarily used for thermal, acoustic, and fire protection in buildings. It is used in residential, commercial, and industrial applications, as well as in HVAC systems and industrial insulation.
-
What are the raw materials for rock wool production?
The primary raw materials are basalt or diabase rock, combined with coke or anthracite as a fuel source for melting. Other additives, such as binding agents, may be used during the fiber formation process.
-
What is the cost of setting up a rock wool insulation manufacturing plant?
The cost of setting up a medium-scale rock wool insulation plant ranges from $3 million to $10 million, depending on factors such as plant capacity, location, and the type of machinery used.
-
Is rock wool insulation environmentally friendly?
Yes, rock wool is made from natural rock and can often contain recycled materials. Additionally, it is a long-lasting insulation solution that contributes to energy efficiency, reducing overall environmental impact.
- What are the fire-resistant properties of rock wool insulation?
Rock wool is highly fire-resistant, withstanding temperatures up to 1,000°C. It is non-combustible and contributes to passive fire protection in buildings.
-
What are the potential profit margins in rock wool manufacturing?
Profit margins in rock wool insulation manufacturing can range from 20% to 40%, depending on production efficiency, market demand, and cost control.
-
How is rock wool insulation packaged?
Rock wool insulation is packaged in plastic wrap or bags to protect it from moisture and contamination. It is labeled for easy identification and shipped in rolls, batts, or boards.
Related Reports
https://www.expertmarketresearch.com/articles/top-5-companies-in-the-global-sodium-glutamate-market
https://www.expertmarketresearch.com/reports/united-states-pizza-market
https://www.expertmarketresearch.com/reports/subscriber-data-management-market
Media Contact:
Company Name: Claight Corporation
Contact Person: Lewis Fernandas, Corporate Sales Specialist — U.S.A.
Email: sales@expertmarketresearch.com
Toll Free Number: +1–415–325–5166 | +44–702–402–5790
Address: 30 North Gould Street, Sheridan, WY 82801, USA
Website: www.expertmarketresearch.com
Aus Site: https://www.expertmarketresearch.com.au