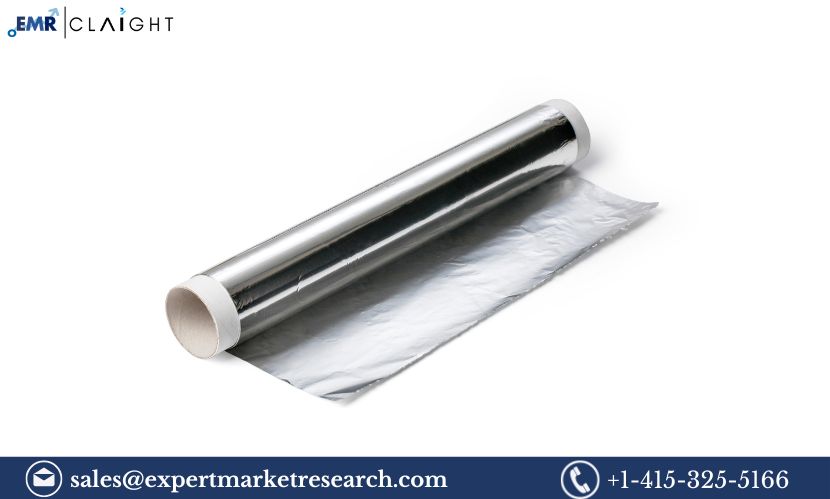
Introduction
The Aluminum Foil Manufacturing Plant Project Report serves as a detailed guide for investors and entrepreneurs looking to establish a facility for producing aluminum foil. With a myriad of applications across various industries, including packaging, food service, and insulation, aluminum foil has become an indispensable material in modern manufacturing. This report outlines essential aspects such as market dynamics, technical specifications, economic feasibility, and operational considerations to ensure a successful venture.
Overview of the Aluminum Foil Industry
Aluminum foil is a thin sheet of aluminum that has numerous applications due to its unique properties, including malleability, lightweight, and resistance to moisture and bacteria. Its versatility makes it a preferred choice in various sectors, contributing to its sustained demand in the market.
Applications of Aluminum Foil
- Packaging: Aluminum foil is widely used in packaging food and beverages to maintain freshness and prevent spoilage.
- Insulation: The construction and automotive industries use aluminum foil for thermal insulation purposes.
- Pharmaceuticals: In the pharmaceutical sector, aluminum foil is employed to package medicines, providing a barrier against moisture and light.
- Household Use: Aluminum foil is a common household item, used for cooking, baking, and food storage.
- Electrical: The electrical industry utilizes aluminum foil in various applications, including capacitors and wiring.
Get a Free Sample Report with Table of Contents@
Market Analysis
The global aluminum foil market has witnessed significant growth, driven by rising consumer demand and advancements in manufacturing technology. Factors such as sustainability, product innovation, and increased industrial applications further propel the market forward.
Key Market Drivers
- Rising Demand for Flexible Packaging: The trend towards lightweight and flexible packaging solutions has boosted the demand for aluminum foil.
- Sustainability: Aluminum is a recyclable material, making it an environmentally friendly choice for packaging, contributing to its popularity.
- Technological Advancements: Innovations in manufacturing processes have enhanced production efficiency and product quality.
Competitive Landscape
The aluminum foil market is characterised by intense competition, with several established players and new entrants. To succeed in this market, companies must focus on quality, innovation, and effective branding.
Project Feasibility Study
Conducting a comprehensive feasibility study is vital for assessing the viability of an aluminum foil manufacturing plant.
Technical Feasibility
Technical feasibility evaluates the production process, equipment requirements, and raw material sourcing.
- Raw Materials: The primary raw material for aluminum foil production is aluminum ingots, which need to be of high quality to ensure optimal foil properties.
- Production Process: The manufacturing process involves several stages, including melting, rolling, and annealing. Each stage requires precise control to achieve the desired thickness and quality of the foil.
- Equipment Requirements: Essential equipment includes melting furnaces, rolling mills, annealing ovens, and cutting machines. Investing in advanced technology is crucial for operational efficiency.
Economic Feasibility
An economic feasibility analysis assesses the financial aspects of the project, including capital investment, operating costs, and revenue projections.
- Capital Investment: The initial investment will cover costs related to land acquisition, facility construction, equipment procurement, and obtaining necessary permits.
- Operating Costs: Ongoing expenses will include raw material procurement, utilities, labor, and maintenance. Effective management of these costs is essential for profitability.
- Revenue Projections: Revenue will depend on market demand, pricing strategies, and distribution channels. Conducting market research to identify potential customers is crucial for accurate revenue forecasting.
Operational Feasibility
Operational feasibility focuses on the practical aspects of running the aluminum foil manufacturing plant.
- Location: Choosing a strategic location is essential for minimizing transportation costs and ensuring easy access to suppliers and customers.
- Workforce: A skilled workforce is necessary for efficient operations. Training programs should be implemented to ensure employees are knowledgeable about production processes and quality control.
- Regulatory Compliance: The facility must comply with local and international regulations governing manufacturing processes, ensuring safety and environmental protection.
Manufacturing Process
The manufacturing process for aluminum foil can be divided into several key stages, each vital for producing high-quality products.
1. Raw Material Preparation
The process begins with the preparation of raw materials, primarily aluminum ingots, which are sourced from reliable suppliers to ensure quality.
2. Melting
Aluminum ingots are melted in furnaces to create molten aluminum, which is then poured into molds for the next stage of production.
3. Rolling
The molten aluminum is rolled into thin sheets using rolling mills. This stage requires precision to achieve the desired thickness and quality.
4. Annealing
Annealing is a heat treatment process that improves the malleability of the aluminum foil. This step is essential for ensuring the foil can be easily shaped and formed.
5. Cutting and Packaging
Once the aluminum foil is produced, it is cut into the desired sizes and packaged for distribution. Proper packaging is crucial for preventing damage during transportation and storage.
Quality Control and Regulatory Compliance
Maintaining high-quality standards and adhering to regulatory requirements are critical aspects of aluminum foil manufacturing.
Quality Control
- Raw Material Testing: All incoming raw materials must undergo rigorous testing to confirm their quality and suitability for production.
- In-Process Monitoring: Continuous monitoring during the manufacturing process ensures that conditions remain optimal for producing high-quality aluminum foil.
- Final Product Testing: The final product must be tested for quality, thickness, and other specifications before it can be released for distribution.
Regulatory Compliance
- Manufacturing Regulations: Compliance with local and international manufacturing regulations is mandatory to ensure the safety and quality of the products.
- Environmental Regulations: Adhering to environmental regulations is important to minimize the ecological impact of manufacturing processes.
Economic Viability
To ensure the economic success of an aluminum foil manufacturing plant, several factors must be considered.
- Cost Management: Implementing cost-effective production methods and optimising resource usage are vital for maintaining profitability.
- Market Positioning: Building strong relationships with retailers and distributors can enhance market positioning and drive sales.
- Innovation: Investing in research and development to create new and improved aluminum foil products can provide a competitive edge.
FAQ
What are the main applications of aluminum foil?
Aluminum foil is used in packaging, insulation, pharmaceuticals, household products, and electrical applications.
How is aluminum foil produced?
The production process involves melting aluminum ingots, rolling them into sheets, annealing, cutting, and packaging.
What raw materials are needed for aluminum foil production?
The primary raw material is aluminum ingots, which are melted and processed to create aluminum foil.
What quality control measures are implemented?
Quality control includes raw material testing, in-process monitoring, and final product testing for specifications.
What regulations govern aluminum foil manufacturing?
Manufacturers must comply with local and international manufacturing and environmental regulations to ensure product safety and quality.
Related Reports
https://www.expertmarketresearch.com/reports/sauces-market
https://www.expertmarketresearch.com/reports/fraud-detection-and-prevention-market
https://www.expertmarketresearch.com/reports/spain-residential-real-estate-market
Media Contact:
Company Name: Claight Corporation
Contact Person: Lewis Fernandas, Corporate Sales Specialist — U.S.A.
Email: sales@expertmarketresearch.com
Toll Free Number: +1–415–325–5166 | +44–702–402–5790
Address: 30 North Gould Street, Sheridan, WY 82801, USA
Website: www.expertmarketresearch.com
Aus Site: https://www.expertmarketresearch.com.au