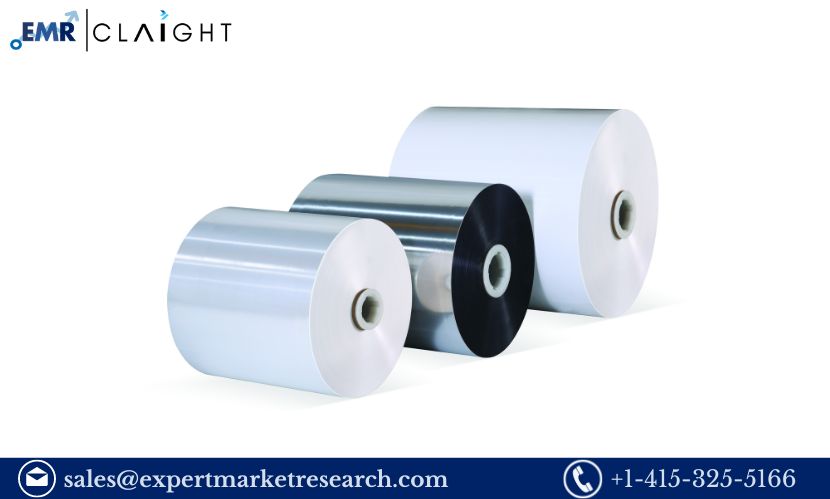
Introduction
The Cast Polypropylene Manufacturing Plant Project Report provides a comprehensive overview of the initiative to establish a facility focused on producing cast polypropylene (CPP), a versatile and high-performance plastic material. This report outlines the key aspects of the project, including market analysis, plant design, raw material procurement, manufacturing processes, and financial planning. CPP is used extensively in various applications, such as packaging and automotive parts, due to its excellent clarity, strength, and flexibility. By detailing the steps involved in setting up and operating a CPP manufacturing plant, this report aims to guide stakeholders through the planning and implementation phases, ensuring a successful and profitable venture in the growing plastics industry.
Key Components of the Project
1. Market Analysis
Before diving into the technical aspects, it’s crucial to conduct a thorough market analysis. This includes:
- Demand Assessment: Understanding the current demand for CPP products in various sectors such as packaging, automotive, and industrial applications.
- Competitor Analysis: Identifying existing competitors and analyzing their market share, strengths, and weaknesses.
- Customer Segmentation: Identifying potential customers, such as packaging companies, automotive manufacturers, and other industries that use CPP.
Get a Free Sample Report with Table of Contents @
2. Plant Design and Layout
The design of the CPP manufacturing plant is a critical aspect of the project. The layout should ensure efficient workflow and space utilization. Key design considerations include:
- Production Capacity: Determining the scale of production based on market demand. This will influence the size of the plant and the number of machines required.
- Equipment Selection: Choosing appropriate machinery for melting, casting, and cooling polypropylene. This includes extruders, casting machines, and winding units.
- Safety Measures: Implementing safety protocols to protect workers and ensure safe operation of machinery.
3. Raw Materials
Polypropylene resin is the primary raw material for CPP production. The quality of the resin affects the final product’s properties, such as clarity, strength, and flexibility. Suppliers should be reliable and able to provide consistent quality.
4. Manufacturing Process
The CPP manufacturing process typically involves the following steps:
- Extrusion: Polypropylene resin is melted and extruded through a die to form a thin film.
- Casting: The molten polypropylene is cast onto a cooling roll or belt to solidify into a thin film or sheet.
- Winding: The cooled film is wound onto rolls for further processing or packaging.
5. Quality Control
Quality control is essential to ensure that the final product meets industry standards and customer requirements. Key quality checks include:
- Film Thickness: Ensuring consistency in film thickness.
- Clarity: Checking for clarity and transparency in the film.
- Mechanical Properties: Testing for strength, flexibility, and other mechanical properties.
6. Environmental Considerations
Implementing eco-friendly practices is increasingly important. This includes:
- Waste Management: Developing strategies for recycling or disposing of production waste.
- Energy Efficiency: Investing in energy-efficient equipment and practices to minimize environmental impact.
- Emissions Control: Installing systems to control and reduce emissions from the manufacturing process.
7. Financial Planning
A detailed financial plan is essential for the success of the project. This should include:
- Capital Investment: Estimating the initial investment required for plant setup, including equipment, construction, and working capital.
- Operating Costs: Calculating ongoing expenses such as raw materials, labor, utilities, and maintenance.
- Revenue Projections: Forecasting potential revenue based on market demand and pricing strategies.
- Profitability Analysis: Assessing the financial viability of the project and expected return on investment (ROI).
8. Regulatory Compliance
Compliance with local and international regulations is crucial. This includes:
- Health and Safety Regulations: Adhering to safety standards for worker protection.
- Environmental Regulations: Complying with environmental laws related to emissions and waste management.
- Quality Standards: Meeting industry standards for product quality and safety.
Challenges and Considerations
- Capital Intensive: Setting up a CPP manufacturing plant requires significant capital investment.
- Market Competition: The presence of established competitors can impact market entry and pricing strategies.
- Raw Material Prices: Fluctuations in the price of polypropylene resin can affect production costs and profitability.
- Technological Upgrades: Keeping up with technological advancements requires ongoing investment and training.
FAQ
What is cast polypropylene?
Cast polypropylene (CPP) is a type of polypropylene plastic that is cast into thin films or sheets. It is used in various applications due to its clarity, strength, and flexibility.
What are the key benefits of CPP?
CPP offers benefits such as high clarity, excellent strength and flexibility, good barrier properties, and resistance to moisture and chemicals. It is widely used in packaging, automotive parts, and other industrial applications.
What are the primary raw materials for CPP production?
The primary raw material for CPP production is polypropylene resin. This resin is melted and cast into thin films or sheets during the manufacturing process.
How do I determine the size of the CPP manufacturing plant?
The size of the plant depends on factors such as market demand, production capacity, and available investment. Conducting a thorough market analysis and financial planning can help determine the appropriate scale.
What are the key quality control measures in CPP manufacturing?
Key quality control measures include checking film thickness, clarity, and mechanical properties such as strength and flexibility. Regular testing and inspections ensure that the final product meets industry standards.
What environmental considerations should be addressed?
Environmental considerations include waste management, energy efficiency, and emissions control. Implementing eco-friendly practices helps minimize the plant’s environmental impact and comply with regulations.
What are the main challenges in establishing a CPP manufacturing plant?
Challenges include high capital investment, market competition, fluctuations in raw material prices, and the need for technological upgrades. Addressing these challenges requires careful planning and strategic management.
Media Contact:
Company Name: Claight Corporation
Contact Person: Lewis Fernandas, Corporate Sales Specialist — U.S.A.
Email: sales@expertmarketresearch.com
Toll Free Number: +1–415–325–5166 | +44–702–402–5790
Address: 30 North Gould Street, Sheridan, WY 82801, USA
Website: www.expertmarketresearch.com
Aus Site: https://www.expertmarketresearch.com.au/