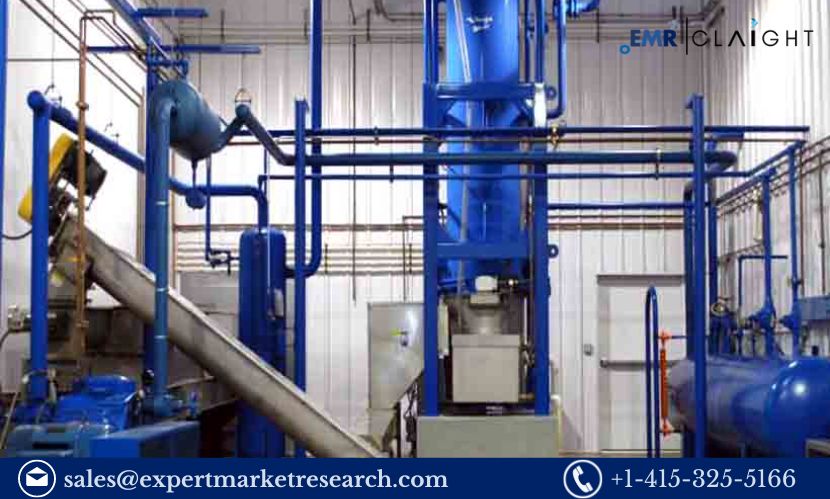
Introduction
Ice manufacturing is a crucial industry supporting various sectors, from food and beverage to healthcare and entertainment. Ice is essential for preserving food, chilling drinks, and even in medical and scientific applications. Setting up an ice manufacturing plant involves a detailed process, including market research, regulatory compliance, and efficient production methods. This article provides a comprehensive Ice Manufacturing Plant Project Report on establishing an ice manufacturing plant, outlining key aspects such as planning, production processes, cost considerations, and frequently asked questions.
Project Planning
1. Market Analysis
Before initiating the project, a detailed market analysis is essential:
- Demand Assessment: Assess the demand for ice in your target market. This includes evaluating the needs of restaurants, bars, food processing industries, medical facilities, and other potential customers. Research market trends, seasonal variations, and growth opportunities.
- Competitive Landscape: Identify existing ice manufacturers and their market share, product offerings, and pricing strategies. Analyze their strengths and weaknesses to understand how to position your plant competitively.
- Regulatory Environment: Understand the regulations governing ice production, including health and safety standards, quality control, and environmental regulations. Compliance with local and international standards is crucial.
2. Site Selection
Choosing the right location for the ice manufacturing plant is vital:
- Proximity to Raw Materials: Select a site close to sources of water, as it is a primary raw material in ice production. Also, consider the proximity to distribution networks to reduce transportation costs.
- Infrastructure: Ensure the site has adequate infrastructure, including utilities (water, electricity), transportation links, and waste management systems. Evaluate the availability of skilled labor and access to maintenance services.
- Regulatory Compliance: The site should comply with local zoning laws, environmental regulations, and health and safety standards. Assess potential environmental impacts and community relations.
Get a Free Sample Report with Table of Contents @
3. Regulatory Compliance
Compliance with regulatory standards is essential for an ice manufacturing plant:
- Health and Safety Standards: Adhere to standards set by health authorities to ensure the ice is produced in a sanitary and safe manner. This includes compliance with FDA regulations or local equivalent standards for food safety.
- Environmental Regulations: Follow regulations related to water usage, waste management, and energy consumption. Implement measures to minimize environmental impact, such as efficient water recycling and energy-saving technologies.
- Quality Standards: Implement quality management systems to ensure the ice meets regulatory and customer standards. This includes regular testing and maintenance procedures.
Manufacturing Process
1. Raw Materials
The primary raw material for ice manufacturing is water. The quality of water is crucial as impurities can affect the clarity and safety of the ice. Other materials include:
- Water Treatment Chemicals: For purifying water and ensuring it meets safety standards.
- Packaging Materials: For storing and transporting ice, such as plastic bags or ice cubes trays.
2. Production Steps
- Water Purification: Treat the water to remove impurities and contaminants. This may involve filtration, sedimentation, and disinfection processes.
- Freezing: The purified water is then frozen using refrigeration systems. Ice can be produced in various forms, including cube ice, flake ice, and block ice. The freezing process involves controlled temperatures and time to achieve the desired ice quality.
- Harvesting and Processing: Once frozen, the ice is harvested from the production unit. Depending on the type of ice being produced, this may involve breaking the ice into smaller pieces or crushing it.
- Packaging: Package the ice in appropriate containers such as bags or trays. Ensure packaging is hygienic and meets regulatory standards for food safety.
- Storage and Distribution: Store the packaged ice in cold storage to maintain its quality before distribution. Implement efficient logistics to ensure timely delivery to customers.
3. Quality Control
Quality control is critical in ice manufacturing to ensure product safety and consistency:
- Water Quality Testing: Regularly test the water for contaminants and ensure it meets safety standards.
- Ice Quality Testing: Inspect the ice for clarity, size, and consistency. Conduct microbiological tests to ensure the ice is free from harmful bacteria.
- Equipment Maintenance: Regularly maintain and calibrate production equipment to ensure optimal performance and prevent contamination.
Cost Considerations
1. Capital Investment
Setting up an ice manufacturing plant requires a significant capital investment:
- Land and Construction: Costs for acquiring land and constructing the facility, including production areas, cold storage, and office spaces.
- Machinery and Equipment: Investment in ice-making machines, water purification systems, refrigeration units, and packaging equipment.
- Technology: Advanced technology for automation, process control, and data management.
2. Operational Costs
Operational costs include:
- Raw Materials: Expenses for water and treatment chemicals.
- Labor: Wages for skilled and unskilled workers involved in production, quality control, and administration.
- Utilities: Costs for water, electricity, and refrigeration.
- Maintenance: Regular maintenance and repair costs for machinery and equipment.
3. Regulatory and Compliance Costs
Additional costs related to regulatory compliance include:
- Certification: Fees for obtaining and maintaining certifications related to food safety, environmental management, and quality standards.
- Safety Measures: Investment in safety equipment and employee training to ensure compliance with health and safety regulations.
- Environmental Management: Costs associated with waste disposal, water recycling, and emissions control.
4. Marketing and Distribution
Marketing and distribution costs cover:
- Promotion: Advertising and promoting ice to potential customers in various sectors.
- Logistics: Managing transportation and storage of finished ice products.
- Customer Support: Providing support and services to clients, including handling inquiries and technical support.
Frequently Asked Questions (FAQ)
1. What Types of Ice Can Be Produced in an Ice Manufacturing Plant?
An ice manufacturing plant can produce various types of ice, including:
- Cube Ice: Standard ice cubes used in beverages.
- Flake Ice: Soft, thin ice flakes often used in food preservation and medical applications.
- Block Ice: Large blocks of ice used in industries or for extended storage.
- Crushed Ice: Ice that is crushed into smaller pieces for use in drinks or cooling applications.
2. How Is Water Purified for Ice Production?
Water is purified using several processes:
- Filtration: Removes particulate matter and sediment.
- Sedimentation: Allows impurities to settle out of the water.
- Disinfection: Uses chemicals or UV light to kill bacteria and pathogens.
3. What Are the Key Considerations for Plant Design?
Key considerations for plant design include:
- Safety: Incorporating safety measures to protect workers and prevent contamination.
- Environmental Impact: Designing facilities to minimize environmental impact, including water usage and energy consumption.
- Efficiency: Ensuring an efficient layout and operation to maximize productivity and minimize costs.
4. What Are the Environmental Impacts of Ice Manufacturing?
The environmental impacts include:
- Water Usage: High consumption of water for ice production.
- Energy Consumption: Significant energy use for refrigeration and freezing processes.
- Waste Generation: Disposal of waste materials and packaging.
Mitigating these impacts involves implementing sustainable practices, such as water recycling, energy-efficient technologies, and proper waste management.
5. How Long Does It Take to Set Up an Ice Manufacturing Plant?
The timeline for setting up an ice manufacturing plant can vary based on factors such as site preparation, construction, and equipment installation. Typically, it takes between 12 to 24 months to complete the setup.
6. What Are the Key Equipment Needed for Ice Manufacturing?
Key equipment includes:
- Ice-Making Machines: For producing different types of ice.
- Water Purification Systems: For treating water before use.
- Refrigeration Units: For freezing water and maintaining cold storage.
- Packaging Equipment: For packaging ice in bags or containers.
7. How Can One Ensure Compliance with Regulatory Standards?
Ensuring compliance involves:
- Training: Providing regular training for employees on regulatory requirements and quality standards.
- Documentation: Maintaining thorough documentation of processes, quality control measures, and compliance.
- Audits: Conducting regular internal and external audits to ensure adherence to standards.
- Expert Consultation: Engaging with regulatory and industry experts to stay updated on best practices and regulations.
Related Reports
https://www.expertmarketresearch.com/reports/sauces-market
https://www.expertmarketresearch.com/reports/fraud-detection-and-prevention-market
https://www.expertmarketresearch.com/reports/spain-residential-real-estate-market
Media Contact:
Company Name: Claight Corporation
Contact Person: Lewis Fernandas, Corporate Sales Specialist — U.S.A.
Email: sales@expertmarketresearch.com
Toll Free Number: +1–415–325–5166 | +44–702–402–5790
Address: 30 North Gould Street, Sheridan, WY 82801, USA
Website: www.expertmarketresearch.com
Aus Site: https://www.expertmarketresearch.com.au