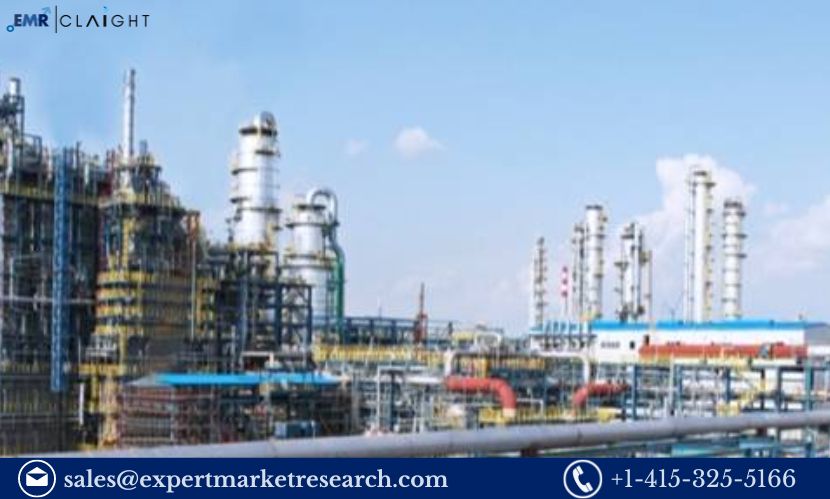
Introduction
Mono Ethylene Glycol (MEG) is a crucial chemical compound used in a wide range of industries, from automotive and textiles to construction and pharmaceuticals. Its primary applications include as a coolant and antifreeze in vehicles, a raw material for producing polyester fibers and resins, and a solvent in various chemical processes. Establishing a MEG manufacturing plant involves a detailed and strategic approach to ensure efficient production, high-quality output, and regulatory compliance. This article provides a comprehensive overview of a Mono Ethylene Glycol Manufacturing Plant Project Report, including key aspects such as site selection, plant design, production processes, quality control, and regulatory considerations. A frequently asked questions (FAQs) section addresses common inquiries related to the project.
Project Overview
1. Objective
The main objective of the Mono Ethylene Glycol (MEG) Manufacturing Plant Project is to establish a facility capable of producing high-quality MEG efficiently and in compliance with industry standards. The plant aims to meet the increasing demand for this versatile chemical by leveraging advanced technology and maintaining stringent quality control throughout the production process.
Get a Free Sample Report with Table of Contents @
2. Site Selection
Choosing the right location for the MEG manufacturing plant is critical for operational success. Key factors to consider include:
- Proximity to Raw Material Suppliers: MEG production requires ethylene and other raw materials. Being close to suppliers can reduce transportation costs and ensure a steady supply chain.
- Infrastructure: The site should have access to essential infrastructure, including reliable power, water supply, transportation networks for shipping products, and communication systems.
- Regulatory Environment: The location should offer a favorable regulatory environment, with streamlined processes for obtaining necessary permits and compliance with health, safety, and environmental regulations.
- Labor Availability: Availability of skilled labor is important for operating and maintaining advanced manufacturing equipment and ensuring adherence to Good Manufacturing Practices (GMP).
3. Plant Design and Layout
The design and layout of the MEG manufacturing plant are crucial for operational efficiency and safety. Key areas of the plant include:
- Raw Material Storage: Secure storage facilities for ethylene and other raw materials, with proper inventory management systems to track usage and maintain quality.
- Production Areas: Dedicated spaces for various stages of MEG production, including reaction, separation, and purification. The layout should optimize workflow and minimize contamination risks.
- Quality Control Laboratories: Equipped with advanced analytical instruments for testing raw materials, in-process samples, and finished MEG to ensure they meet quality standards.
- Packaging and Distribution: Areas for packaging MEG into various formats (e.g., drums, bulk containers) and preparing them for shipment to customers, ensuring product protection and compliance with labeling regulations.
- Utilities and Waste Management: Facilities for managing utilities such as power and water, as well as handling waste products in compliance with environmental regulations.
4. Production Process
The production process for MEG involves several key stages:
- Feedstock Preparation: Ethylene and other feedstocks are prepared and pre-treated for the production process.
- Reaction: Ethylene oxide (EO) is reacted with water in a controlled process to produce MEG. This typically occurs in a high-pressure reactor.
- Separation and Purification: The reaction mixture is separated to isolate MEG, and impurities are removed through various purification techniques, including distillation and filtration.
- Finishing: The purified MEG is further processed to achieve the desired purity and quality.
- Packaging: The finished MEG is packaged into drums or bulk containers for distribution and sale.
5. Quality Control
Ensuring the quality of MEG is essential for its effective use in various applications. Key quality control measures include:
- Raw Material Testing: Verifying the quality and suitability of ethylene and other raw materials before they are used in production.
- In-Process Monitoring: Regular checks during the reaction, separation, and purification stages to ensure adherence to specifications and prevent deviations.
- Finished Product Testing: Comprehensive analysis of the final MEG to ensure it meets required specifications for purity, concentration, and safety.
6. Regulatory Compliance
Compliance with regulatory standards is crucial for operating an MEG manufacturing plant. This includes:
- Good Manufacturing Practices (GMP): Adhering to GMP guidelines to ensure that the manufacturing process is consistent and controlled, resulting in high-quality products.
- Environmental Regulations: Managing waste, emissions, and resource use in compliance with local and international environmental regulations to minimize the plant’s ecological footprint.
- Health and Safety Standards: Ensuring that the plant meets health and safety regulations to protect workers and maintain safe operating conditions.
7. Economic and Environmental Considerations
Setting up an MEG manufacturing plant involves a significant capital investment in infrastructure, equipment, and operational costs. However, the potential for substantial returns through product sales and market expansion makes it a viable investment. Environmentally, implementing sustainable practices such as energy-efficient technologies and effective waste management can help reduce the plant’s ecological footprint and enhance its sustainability.
FAQs
1. What is Mono Ethylene Glycol (MEG) used for?
Mono Ethylene Glycol (MEG) is used in a variety of applications, including as an antifreeze in automotive engines, a raw material for producing polyester fibers and resins, and a solvent in chemical processes.
2. What are the main stages of MEG production?
The main stages of MEG production include feedstock preparation, reaction (ethylene oxide with water), separation and purification, finishing, and packaging.
3. How do I choose the right location for an MEG manufacturing plant?
Choosing the right location involves factors such as proximity to ethylene and other raw material suppliers, availability of infrastructure and skilled labor, favorable regulatory environment, and environmental impact considerations.
4. What are Good Manufacturing Practices (GMP) in MEG production?
Good Manufacturing Practices (GMP) are guidelines that ensure the manufacturing process is consistent and controlled, resulting in high-quality products. GMP includes equipment maintenance, process control, and employee training.
5. What quality control measures are necessary for MEG production?
Quality control measures include testing raw materials, monitoring in-process production, and conducting comprehensive tests on the finished MEG to ensure it meets specifications for purity, concentration, and safety.
6. How can an MEG manufacturing plant minimize its environmental impact?
An MEG manufacturing plant can minimize its environmental impact by implementing energy-efficient technologies, reducing waste, controlling emissions, and adhering to environmental regulations.
7. What is the typical timeline for setting up an MEG manufacturing plant?
The timeline generally includes phases for planning and design, construction and equipment installation, validation and commissioning, and production start-up, spanning approximately 18-24 months.
8. What are the economic benefits of an MEG manufacturing plant?
Economic benefits include job creation, increased industrial output, and potential revenue from product sales. A well-managed plant can significantly contribute to the local economy and provide a strong return on investment.
Related Reports
https://www.expertmarketresearch.com/articles/top-6-companies-in-the-global-peppermint-oil-market
https://www.expertmarketresearch.com/reports/pharmaceutical-contract-packaging-market
https://www.expertmarketresearch.com/articles/top-india-furniture-companies
Media Contact:
Company Name: Claight Corporation
Contact Person: Lewis Fernandas, Corporate Sales Specialist — U.S.A.
Email: sales@expertmarketresearch.com
Toll Free Number: +1–415–325–5166 | +44–702–402–5790
Address: 30 North Gould Street, Sheridan, WY 82801, USA
Website: www.expertmarketresearch.com
Aus Site: https://www.expertmarketresearch.com.au